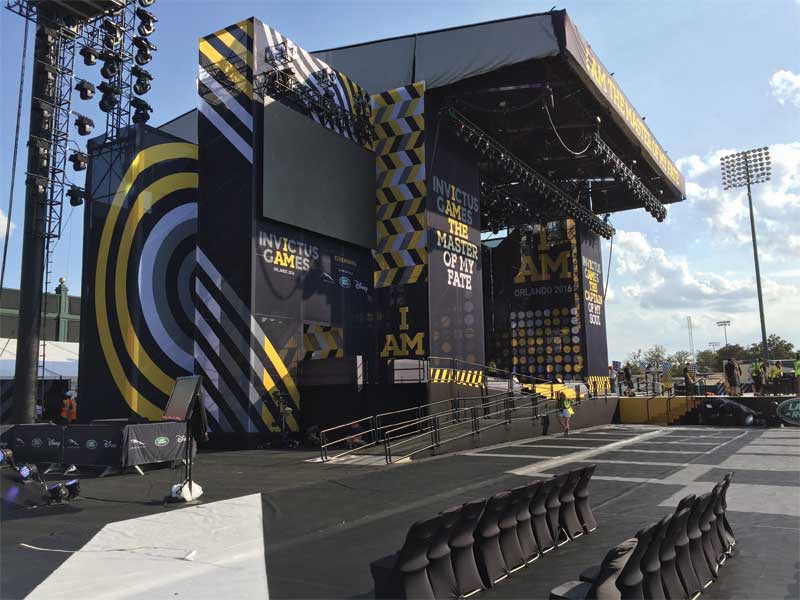
The market is booming for ‘soft signage,’ such as these fabric graphics produced for Toronto’s 2017 Invictus Games.
Photo courtesy PNH Solutions
Echoing ISA, Smithers Pira highlights digital textile printing as one of the most significant market opportunities, with double-digit growth. In another report, The Future of Digital Textile Printing to 2021, the company forecasts an average annual growth rate of 12.3 per cent and expects the global market to more than double in value over five years, to nearly US$2.7 billion in 2021. And based on a comprehensive survey of printing equipment and inks, Smithers suggests the volume of fabric printed with digital inkjet systems will increase from 870 million m2 (9.36 billion sf) in 2016 to 1.95 billion m2 (21 billion sf) in 2021, representing a CAGR of 17.5 per cent.
Soft signage and displays are expected to maintain double-digit growth across the study period, for the largest absolute increase in value, but even greater acceleration is forecast for clothing and household textiles. And while digital processes’ share of the overall textile market’s value was only 2.8 per cent in 2016, it is set to boom compared to the industry’s mean growth rate of just three per cent.
As this trend continues, major print service providers (PSPs) are purchasing existing textile printing businesses, while manufacturers are developing new printheads, inks, media and high-throughput presses. Further, global textile industry dynamics are changing as digital automation allows production to be ‘backshored’ or ‘reshored’ to such regions as North America and Europe for high-value applications.
“Near-exponential growth cannot be sustained in the long run as a market matures, but several very high-growth regions remain to be tapped,” explains associate consultant Justin Hayward, who wrote the report. “The revolution digital printing has created in graphics shows a market penetration of over 70 per cent can occur within a few years if there is extensive cost parity and if barriers to change are removed.”
Digital printing can produce single, short and custom runs much faster and more economically than conventional screenprinters. As the capabilities of digital textile presses dovetail with the priorities of customers for printed fabrics, such as fashion designers, Smithers Pira suggests new ‘value-add’ business opportunities are being created for both PSPs and material suppliers.
Its report shows only 2.9 per cent of the 30 billion m2 (323 billion sf) of textiles printed in 2016 was produced using inkjet equipment, while the rest was principally produced using screenprinters. The digital share has grown rapidly in recent years, however, from 461 million m2 (5 billion sf) in 2012 to 870 million m2 (9.4 billion sf) in 2016. It is expected to break through 1 billion m2 (10.8 billion sf) before the end of 2017 and then nearly double to 1.95 billion m2 (21 billion sf) in 2021. Smithers Pira forecasts the corresponding revenues will grow by 15.7 per cent year-on-year, compared to an average growth rate of just three per cent for all printed textiles.
With conventional processes threatened, global firms are investing in digital textile printing technologies. Dover Group, for example, now encompasses press manufacturer MS Printing Solutions and textile ink formulators Sawgrass Industrial, Kiian Digital and J-Teck3. EFI acquired Reggiani in 2015, then partnered with DuPont to develop pigment-based textile inks. In 2016, Mimaki purchased La Meccanica and Epson acquired Robustelli.
These and other manufacturers are developing and refining their printhead-ink-media combinations to enable higher throughput, greater reliability and stability. With the resulting, simplified processes, PSPs can tailor their offerings to designers who want a variety of detailed shapes and colourful patterns.
Incremental improvements have been made to ink formulations, dispersions and pigment particulates, driven by the demand to print on multiple fabrics. The machinery developments, meanwhile, have focused on individually addressable ink nozzles, the elimination of banding and the handling of fabric tension during printing. New single- and multiple-pass printers continue to come to market from various manufacturers, including compact machines that require less floor space, which may see rapid adoption among PSPs that specifically serve the fashion industry.