By Mike Santos
The use of braille dots on accessibility signage has gotten a lot of attention in recent years across the sign industry. Most accessibility signs identify a room or a space in a public facility where it is important to assist visitors in finding their way, including those with visual impairments.
In the U.S., all public facilities must comply with the 2010 Americans with Disabilities Act (ADA) Standards for Accessible Design (SAD). These standards include accessibility code requirements for braille on signs identifying all permanent rooms, along with other requirements governing colour contrast, mounting heights and other specifications.
In Canada, while there have been provincial efforts like the Accessibility for Ontarians with Disabilities Act (AODA), there is no enforceable national code for accessibility. This has not stopped overall progress, however, and many new facilities across Canada are being built with accessibility signage for room identification and wayfinding.
With a growing focus on accessibility has come innovation in sign materials. All facilities need signs anyway and making them accessible does not necessarily add much difficulty, but if the proper materials are used, they can enhance a facility’s overall design while ensuring a smooth navigational experience for all occupants.
Over the years, photopolymers—light-sensitive resins that harden when exposed to ultraviolet (UV) light—have emerged as the new industry standard in this respect. The unexposed sections of the resin dissolve in water during a washout process, leaving behind the raised elements, such as text and braille.
For today’s photopolymer signs, graphics are first created in a digital format, then a film negative is generated before the material is processed with UV light and water. Once the material has been processed, signs can be fabricated and decorated with the same conventional methods used for other typical substrates, including cutting, routing and painting.
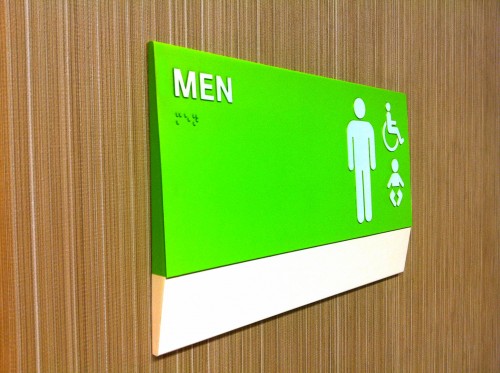
Photopolymer resins enable control of the relief depth of raised elements, including text, braille dots and pictograms.
A photo finish
ADA, especially, was a major initiative to improve the lives of people with disabilities. The sign business was one of many industries affected by the new laws. For the first time, all public facilities across the U.S. needed to include braille text and tactile copy and graphics on their permanent room signs.
Photopolymer substrates were introduced to sign shops shortly after the original passing of ADA in 1991. They quickly gained favour for use in accessibility signs around the world.
Prior to 1991, photopolymers were used to produce high-quality graphics in flexographic and letterpress printing. The same photopolymer plates used for letterpress printing turned out to be ideal sign substrates, as many of them had a very hard durometer, were processed in plain tap water and were exposed to UV light for processing. As the photopolymer resin was extruded to the surface of a base substrate, it allowed control of the relief depth of raised elements, including text, braille dots and pictograms. With a few simple modifications to the resins, a new process was born for the sign industry.
The conversion of letterpress plates into accessibility signage substrates proved an overnight success, enabling sign fabricators to efficiently produce the high-quality pieces required to comply with ADA and similar regulations around the world, keeping up with rising demand.
In the earliest days of ADA, the photopolymer substrates had a thin aluminum backing, so the signs needed to be surface-painted. While they could feature tactile images, borders and logos, there was no way yet to incorporate any digitally printed graphics or simulate the appearance of other materials used in the same facility.
By the mid-1990s, photopolymers became available on a thicker phenolic backing. This did not enable more design options per se, but it did eliminate the need for additional mounting material to achieve the desired sign thickness, so it quickly became an industry-standard material.
In 1999, new clear photopolymer resins were mounted onto polyethylene terephthalate glycol (PETG) substrates and offered in a variety of base thicknesses. These materials spawned a new generation of accessibility signage. For the first time, fabricators could use a broad variety of design techniques and incorporate digitally printed graphics with braille dots and other raised elements on their accessibility signs.