By Ed Kiyoi
The wide-format printing sector is familiar by now with ultraviolet (UV) curing, which has allowed compatible inks to be instantly polymerized during the printing process, rather than rely on more traditional solvent-based inks, which must be allowed to dry and off-gas after printing. More recently, however, another game-changer for specialty graphic applications has been the use of light-emitting diodes (LEDs) for UV curing, instead of arc lamps.
LEDs open new possibilities for UV curing, including the printing of thinner and heat-sensitive materials, as LEDs run cooler than arc lamps. They can also be integrated into slimmer, more compact machines, will last longer with less need for maintenance and will save electrical costs through their greater energy efficiency. Further, LEDs contain no hazardous mercury or ozone and they emit UV light within a safer wavelength range than arc lamps do.
For LEDs to compete with arc lamps in the wide-format printing sector, of course, they have had to progress to the point where they can cure inks just as effectively, with a reliable breadth of UV light. The irradiance output of LEDs has certainly increased significantly over time, but more relevant to UV curing have been the design innovations in LED arrays, optics and thermal management that have enabled an increase in total UV output.
LEDs are semiconductors. Like most electronics in general, they need to be kept cool to ensure their reliability, performance and lifespan, so the design of the UV curing system must account for thermal management.
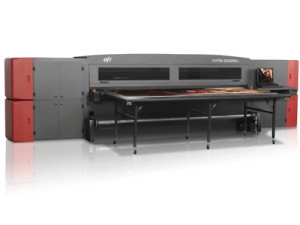
In 2011, EFI integrated UV LEDs in its Vutek GS3250LX printer. Fogra assessments showed the machine reduces engery use by up to 82 per cent compared to printers using conventional mercy arc UV lamps.
It has helped that wide-format printer manufacturers have worked closely with ink formulators to optimize UV LED curing. No longer merely an ‘emerging’ technology, there have been multiple successful deployments over the years, with a myriad of benefits.
Indeed, there is widespread adoption today of UV LEDs compared to just a few years ago, with ink formulators, printer manufacturers and print service providers (PSPs) working together to advance the technology.
Formulating inks
Advances in UV-curable ink formulations have also helped make UV LEDs a viable alternative to medium-pressure mercury lamps.
UV light triggers photoinitiators in inks to create ‘free radicals,’ which connect with molecules in resins and monomers to form cross-linked chains of molecules that comprise a cured ink film (see Figure 1). For the inks to cure properly, they must be exposed to a sufficient amount of energy in the correct wavelength ranges. This amount of energy is called the ‘dose’ and is measured in millijoules per square centimetre (mJ/cm2). The dose is affected by the printer’s conveyor or belt speed and the number of times the ink is exposed to the UV LEDs.
Until recently, UV-curable screenprinting inks did not offer sufficient processing latitude for compatibility with the relatively low wattage and narrow wavelength ranges of UV LEDs. Today, however, companies like Nazdar have adopted new technologies and developed screen inks that can be cured by LEDs to create graphics. The curing speed range is directly related to the colour of the ink and the substrate, as well as the ink deposit level.
As mentioned, UV LEDs also offer an opportunity for safer and more environmentally friendly printing. Inks developed for GCC’s StellarJet large-format printer, for example, are not only free of hazardous volatile organic compounds (VOCs), but also use special chemicals to eliminate potential irritants to machine-operating personnel.