By Ken VanHorn and Tommy Martin
In the wide-format digital printing industry, the term ‘textile’ has been used to encompass a variety of applications, materials and processes, including wearables, soft signage, interior décor, environmental graphics and other applications using dye sublimation, direct-to-fabric printing or another transfer process.
Both dye sublimation and direct-to-fabric processes have seen a resurgence in recent years, driven by the larger shift from traditional analogue screenprinting to digital wide-format printing. Today’s inkjet printing options for textile-based interior décor and soft signage applications include solvent-based, ‘eco-solvent,’ durable aqueous ‘latex’, ultraviolet-curable (UV-curable) and even solvent UV inks.
Different printing technologies offer different strengths and are suitable for different applications. Signmakers need to understand these processes from the perspective of the specific inks.
Dye sublimation inks
Also called ‘dispersion inks,’ dye sublimation inks yield vibrant colours that can stand up to repeated washing. They are limited to printing on polyester-based or polymer-coated materials and offer lower outdoor longevity than some of the other options. As such, they are primarily used in the active sportswear and exhibit graphics markets.
Typically, but not always, dye sublimation inks use a transfer process, i.e. they are printed to an inexpensive paper before they are transferred to a textile substrate. In the post-printing step, the printed transfer paper roll is aligned to the ‘accepting’ fabric roll and the two are then processed together in a calender heat press for 30 to 45 seconds at high temperatures, up to 204 C (400 F).
The transfer process allows users to sublimate not only polyester-based textiles, but also a wide range of polyester-coated rigid substrates, including unusual shapes like coffee mugs. The transfer paper itself is relatively easy to handle and the resulting graphics can convey sharp colours and clear images.
Dye sublimation inks can also be printed directly onto fabrics, eliminating the need for transfer paper and reducing the number of steps in the overall process; but the fabrics for direct printing need to be coated, which increases their cost, and post-processing is required to set the dyes. Choices are also reduced, as coated fabrics are limited in terms of both type and weight. Further, wide-format graphics printed directly to fabrics do not appear as sharp and their colours do not ‘pop’ as much as with transfer-based sublimation.
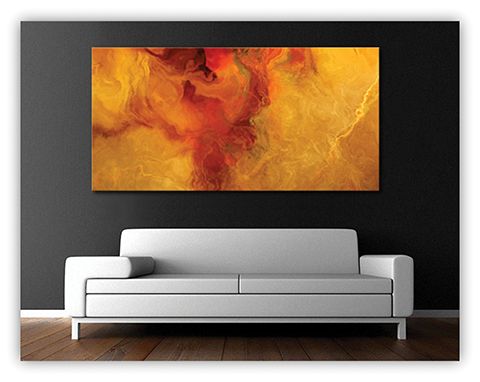
Interior décor applications can be printed with dye sublimation, durable aqueous ‘latex’ or solvent-based ultraviolet-curable (UV-curable) inks.
Reactive inks
Reactive inks involve a chemical process using a molecular dye that yields excellent washable durability and lightfastness for such applications as home furnishings. The inks can be printed onto pretreated natural-fibre textiles, such as cotton, linen, silk, rayon, hemp, viscose (wood cellulose) and bamboo.
Once printed, the fabric must be steamed and washed. The steaming process is important to cure and set the dyes in the fabric. Depending on the type of steamer used, this process will take anywhere from 10 to 20 minutes. The washing, meanwhile, is necessary to clear off any uncured ink or coating, which is especially important for bed linens and apparel.
No detergents or chemicals are needed for the washing process, just hot water and time to dry the fabric. This process will add a soft hand back to the fabric that was lost to precoating.