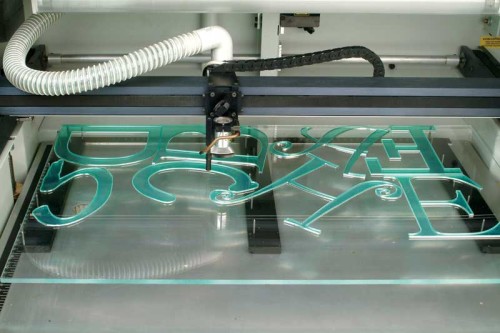
Photos courtesy Gravotech
By Robert Hernandez, Anthony Harris and Terri Bristow
Engravers can help improve a sign shop’s productivity, efficiency and profit margins. They handle work that would otherwise need to be outsourced, for example, and they enable new revenue streams by allowing shops to offer new products to their existing customers. With the enhanced graphic capabilities of three-dimensional (3-D) design software, engravers not only expand upon a shop’s past capabilities, but also enhance its workflow and allow it to respond to last-minute opportunities with better control of finished product quality and delivery.
One of the first challenges, however, is to choose between a laser or rotary engraving machine. This will depend on which technology best meets a specific sign shop’s needs, so it is important to explore the differences between them.
Laser
Laser engraving is the preferred process for cutting acrylic for dimensional letters, signs and architectural elements with a flame-polished edge. Its ability to control fine-detail product quality makes it well-suited for cutting tactile lettering for accessibility signage and inlays, without the need to clean up chips after processing.
Laser engravers excel at productivity, achieving processing speeds up to 4 m (157 in.) per second. They are well-suited for producing large quantities of small items—such as name badges—at the same time and enable fast collection of the cut pieces.
In addition to acrylic, wood and other rigid sign materials, they offer the versatility of cutting fabrics and papers. Some sign materials, such as Lexan polycarbonate, do not lend themselves to laser engraving and will end up with tanned or browned edges. Laminated plastics can show a ‘smoke trail.’ While the level of heat relates directly to the creation of burn marks, ultimately the material itself determines the finish.
Larger laser machines can accommodate full-size sheets of engravable materials, with pass-through options that allow for the processing of oversized sheets. One of the issues in this regard is safety. Class 1 offers the safest configuration, whereby the laser is contained within a protective cabinet and the operator cannot be exposed directly to it. This has proven popular with small to midsized sign shops.
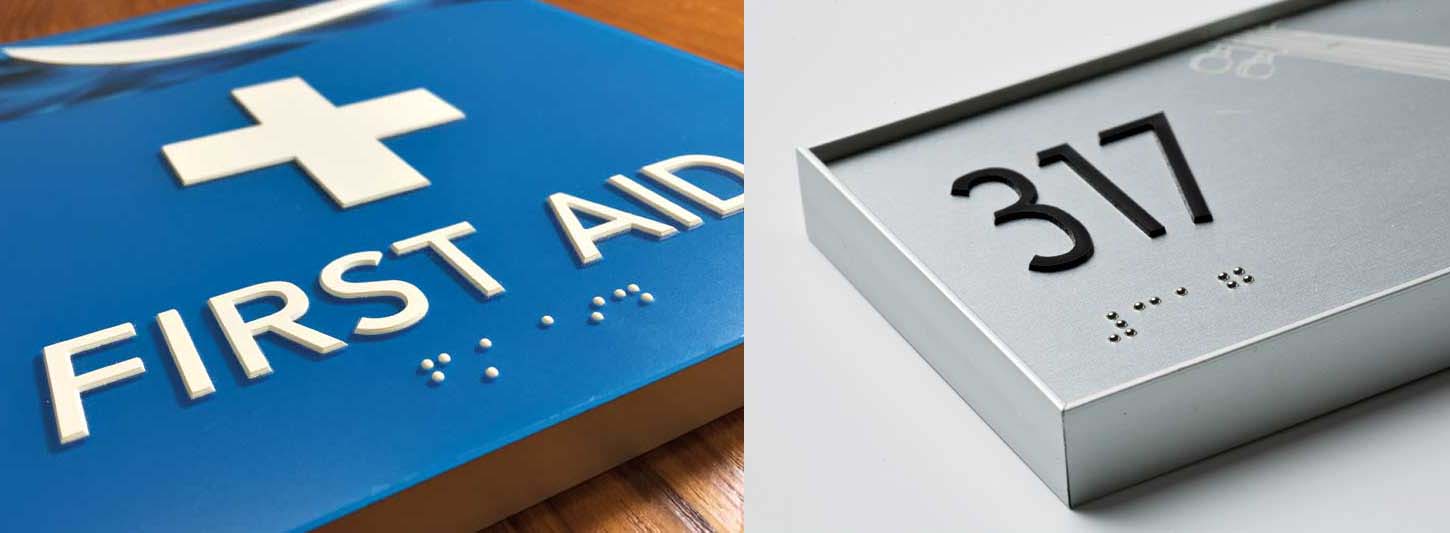
Rotary engraving machines have significantly increased productivity for braille signs.
With Class 4, on the other hand, the safety precautions are removed by opening the engraving machine’s panels to accommodate oversized materials. The machine can still be safe to use, as long as the operator has received additional training. For this reason, it is common to set up security codes, so only the more seasoned operators can access a Class 4 configuration when needed.
The accompanying software can help increase efficiency through ‘nesting.’ This is the process of maximizing the use of the material for the least amount of waste. The optimization of the toolpath is automated and the production time is minimized, too. Nesting can also be used when registering and laser-cutting printed media.
Lasers also enhance graphic capabilities, as they can process high-resolution raster images, photos and special elements like Quick Response (QR) codes, unique device identifiers (UDIs) and bar codes. They can also be deployed for intricate specialty design projects, enabling greater creativity and commanding a premium price. And compared to rotary engravers, they require fewer consumables.