By Peter Saunders
As the market for ultraviolet-curing (UV-curing) flatbed printers has expanded, many new opportunities have arisen with the introduction of energy-efficient light-emitting diodes (LEDs) to these machines. Using LEDs for the graphic curing process, rather than mercury vapour lamps, limits the reactivity of the inks and is better-suited to low-productivity systems than to high-productivity grand-format inkjet printers, but it also expands the range of applications these already versatile systems can accomplish.
Raising the bar
Moving beyond the printing of flat sign graphics on rigid substrates like acrylic, UV-LED curing and compatible inks are enabling direct-to-substrate graphics on everything from T-shirts to smartphone cases to golf balls to bottles and tubes. And within the sign industry, they can add texture to created raised elements, such as braille dots on accessibility signage.
Textured and ‘raised-object’ printing has been achievable with direct-to-substrate UV-LED printing for quite some time, but it has been a challenge to make sure the results are durable enough for long-term accessibility signs and comparable applications. It is also important to have all of the proper components in place to make raised printing efficient within a busy production environment.
Curing in place
Advanced software and hardware are needed to work simultaneously to operate the inkjet printheads for a UV-LED printer. Specially formulated inks are jetted in the areas designated by the raster image processor (RIP) software, followed closely by the UV light that cures the inks in place, producing a dry and durable image.
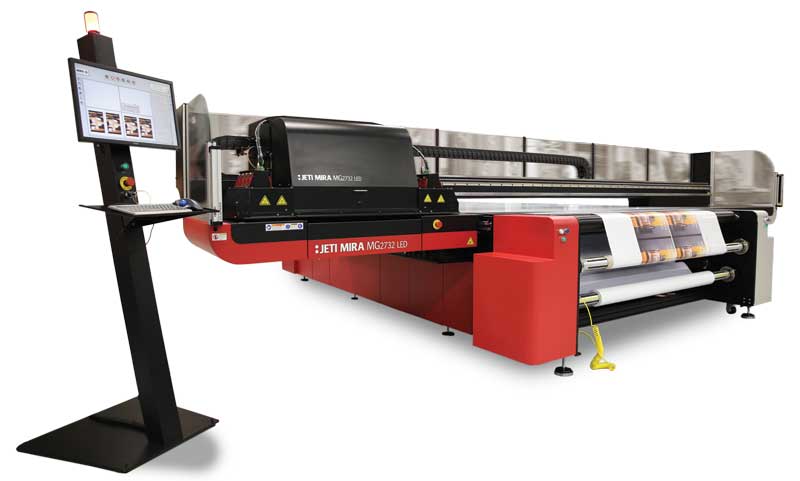
Some wide-format UV-LED flatbed printers can apply a three-dimensional (3-D) primer or varnish.
Photo courtesy Agfa Graphics
This process works on many types of surfaces. The fact the image can be cured in place allows for the jetting of the large volumes of ink that are necessary to build up the texture on the substrate. Indeed, multiple layers can be added simultaneously, creating a thick buildup of ink that is similar to plastic after it has been cured, in any colour or shape that may be desired.
There is also almost no setup time required. Any of a multitude of substrates of varying shapes and sizes can be placed on the flatbed table in the proper position, which is usually predetermined by the combination of (a) a fixture and (b) a template within the software. Then it is simply a matter of hitting ‘print’ and watching as the artwork is printed directly onto the product. At the end, the product comes off the machine ready for sale to the end user.