Wide-format Printing: Maximizing the potential of colour
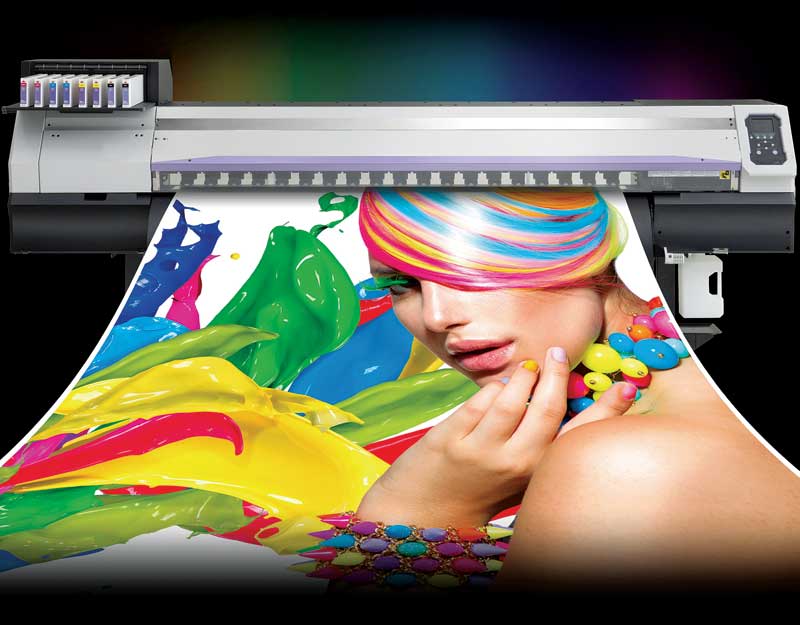
By Josh Hope
There are numerous ways to maximize the potential of colour in wide-format printing, including taking advantage of today’s expanded colour ink sets and better understanding the nature and role of input profiles.
Expanded colour ink sets
Adding new ink sets to a print production department is a great way to expand its output gamut and successfully produce challenging colours. The inks themselves, however, are only half the battle. To get the maximum value out of them, the process of extending beyond the standard cyan, magenta, yellow and key/black (CMYK) space also requires planning and attention to how image files are set up.
A standard CMYK workflow, particularly a raster-based one, will not allow the files to request expanded colours from an output device without some additional steps. The default CMYK colour space in Adobe’s Photoshop software, for example, is U.S. Web Coated Specifications for Web Offset Publications (SWOP), which is very limited when compared to the scope of an expanded-gamut inkjet printer.
For the sake of illustration, one could think of the US Web Coated SWOP CMYK colour space as a 473-ml (16-oz) glass of water and a CMYK-plus-orange output device as a 710-ml (24-oz) empty glass. If the water is poured into the larger glass, there will still be one-third of the glass left empty; it cannot be filled. To take advantage of the larger gamut of the output device, there also needs to be a larger colour space at the design stage.
Depending on the specific workflow, there are a few ways to achieve this. One is working in red, green and blue (RGB), if the raster image processor (RIP) software supports it, as then the files can request the larger gamut of the output device. The old-school practice of converting files from RGB to CMYK before using the RIP was sensible in the days of offset presses, but is usually not necessary in an all-digital workflow. Becoming proficient at making edits in RGB can take some getting used to, but the results can be well worth the effort. For vector-based artwork, colour swatches can be defined in RGB, as well, and will reap the same benefits.
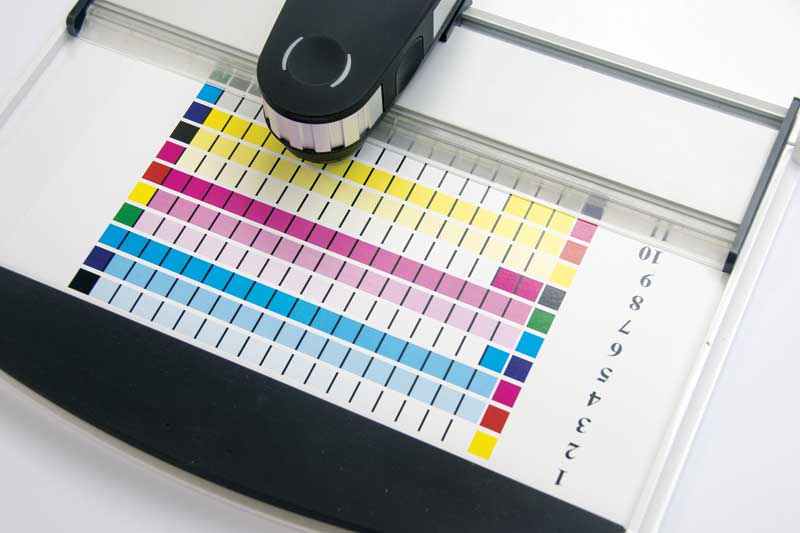
If, on the other hand, the raster files must be defined in CMYK, then it may be worth considering standardizing the workflow with the new Expanded CMYK (XCMYK) colour space, developed by the International Digital Enterprise Alliance (IDEAlliance) for four-colour presses and released at the end of 2016. While this data set will still not completely cover the gamut of a printer with orange and/or green inks, it is significantly larger than the default US Web Coated SWOP colour space. It can be downloaded from IDEAlliance’s website (www.idealliance.org) and set as the new default CMYK colour space in Adobe Photoshop or other image editing software.
An even more powerful way for files to request an expanded gamut from a printer is to use colour book swatches defined by L*a*b* values. If the RIP software supports colour books or named colours with L*a*b values, this is probably the best way to take full advantage of the printer’s and the inks’ potential.
By requesting a colour via L*a*b* values, the workflow effectively bypasses any constraints on the design document colour space. When the named colour is correctly referenced in the RIP (which should be checked in the RIP’s colour library), the colour values can be converted directly through the output profile of the device and to a known print condition. Assuming the output profile is accurate, this will ensure the full benefits of the additional ink colours can be exploited.
Yet another way to address additional ink sets is through a direct colour replacement. If a specific design file colour is selected at the RIP stage of the workflow, then it can often be mapped directly to an ink value. By way of example, if a solid magenta square is selected in a design file, then it can be replaced in the RIP software with 100 per cent orange ink or with a mix of orange and other ink colours. Some RIPs only allow this type of replacement to be achieved within vector-based artwork, but others support it in raster-based files, as well.
To make the process simpler, some printer manufacturers provide a colour swatch library that matches up with another predefined colour library within the RIP. In any case, users are advised to read their RIP software manual to see what options are available and then experiment to achieve the best results.