CNC Routers: Five tips for getting the best cut
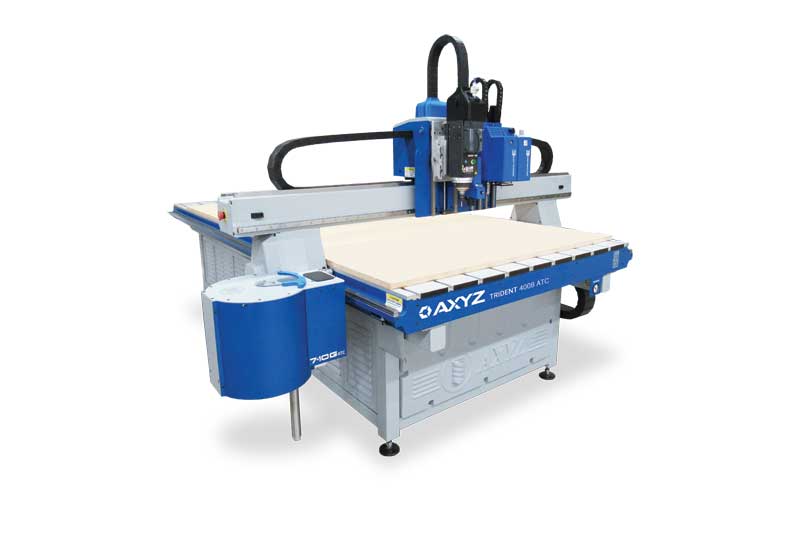
By Susan Mattine
Learning how to customize and configure a computer numerical control (CNC) router for the first time can be a time-consuming and confusing process. Watching small pieces fly off the machine or fabricating parts with rough edges are common issues for novice users. Workarounds or makeshift solutions might be a temporary answer, but what about in the long run? In these cases, it is important to seek assistance from a reputable CNC manufacturer for technical guidance. Vendors often attend trade shows, hold open houses, and give live demonstrations on their machines. Watching a CNC router in action is a great introduction to manufacturing automation. When one is ready to invest in this equipment, it is a good idea to choose a vendor that offers training and post-sales service. These are the vendors signmakers can trust to help take their sign and graphics business to the next level.
In the meantime, it is important one conducts the proper research to become familiarized with all things CNC-related. When one is all set to go, the following five tips for successful CNC routing should be considered.
1. Purchase a CNC hybrid to maximize versatility
CNC hybrids are becoming increasingly popular as a niche technology because of their versatility. For instance, one can produce dimensional signage one day, acrylic letters the next morning, and print-to-cut graphics that afternoon—all on the same machine.
The key to this versatility is in the design and engineering of hybrids, which can accommodate both standard router bits that are typically used for hard materials and knife cutters for softer ones. With only minimal set-up time, the router itself can switch from one type of cutter to another, after being programmed.
Installing a CNC hybrid can make a lot of sense for sign companies, particularly smaller shops where floor space is at a premium, and capital expenditures are made with utmost caution.
2. Preserve tool life by implementing a two-part cutting process
Experienced CNC machinists often split the cutting process into two parts—a roughing cut and a finishing cut—each completed using a different tool. This preserves the finishing tool longer, which in turn enables a higher quality finish. For instance, this technique should be used when cutting acrylic for retail or other type of display work, as it is critical to achieving the best edge while preserving tool life. Time is also saved on each project as the finishing tool does not need to be changed. To further maximize tool life, a polycrystalline diamond (PCD) tool may be used, which can easily achieve two to three times the tool life of regular carbide tools.
The roughing cut does the majority of the work, reducing the load on the finishing cut. The roughing pass churns out most of the material, whereas the newer finishing cutter removes the remaining material and leaves a smooth, polished edge.