By Eve Padula and Steve Urmano
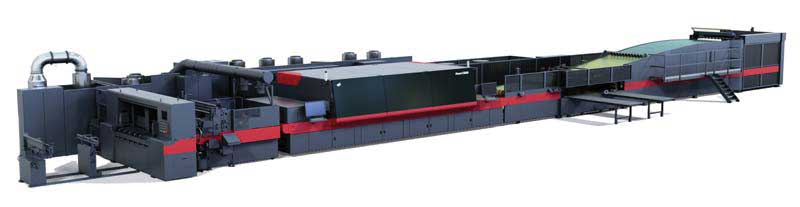
Fuelled by the ongoing success of multi-pass devices and the more recent introduction of single-pass machines, the corrugated market continues to grow.
Although corrugated materials have been around for more than a century, their uses continue to evolve as technologies improve and market demands change. The traditional cardboard box is likely the first thing that comes to mind when most people think about corrugated, but the overall market is actually much larger. Today’s corrugated packages come in a limitless variety of shapes and sizes, and free-standing/point-of-purchase (POP) displays are also part of this category. Food and beverage manufacturers have been—and will remain—huge consumers of corrugated packages as they strive to differentiate their products, protect the contents, maintain freshness, and increase awareness for their brands. The need for packaging grows with the human population and economic development, and this is one industry that is not being displaced by electronic offerings.
While market maturity and increased competition from other forms of packaging do pose some threats, the corrugated industry continues to grow. Further, the recent movement toward digital printing has created many new strategic opportunities in the marketplace.
This white paper evaluates the emerging applications and opportunities in the corrugated space and considers the role digital inkjet will play today and in the future.
Market overview
Background
Since many purchasing decisions are made based on the appearance of a package or the signs/displays in a retail environment, it is important to design materials that send the right message to prospective buyers. Printed graphics can be applied to corrugated boxes, displays, or signs in one of two ways:
• Images, text, and designs can be directly printed on board materials after the board is combined and cut into sheets. For a more refined result, images can also be directly printed onto the linerboard before it is glued to the fluted (corrugated) medium.
• Sheet printing involves outputting on separate sheets that are then glued to combined board. This printing process can be achieved in two ways:
ii. Single-face lamination involves laminating a prepared sheet directly to the open flutes of a single face.
ii. Labelling combined board, also referred to as litho labelling, is printing on a sheet of paper or label stock that is later glued to the combined board.