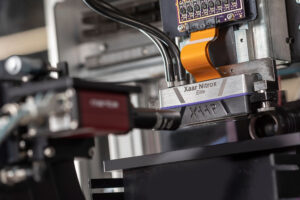
An example of a present-day printhead in operation.
By Graham Tweedale
Over the past few years, inkjet has taken giant leaps into many areas of printing—from graphics and large-format signs to new applications, such as printing on a wider variety of surfaces for decoration (glass, ceramic tile), manufacturing processes (printed electronics), and 3D additive manufacturing.
However, with these new applications have come new challenges. People continue to push the boundaries of what can be printed via inkjet, which often requires fluids that are more viscous, have higher particle loading, and thus are more challenging to lay down. Inkjet printing also means working with fluids ranging from oil-based and solvent to aqueous.
For the inkjet process to work effectively, printheads need to deposit these inks and fluids reliably and at acceptable speeds. Further, printheads must be resistant to any damaging properties of these inks. How have they stepped up to the challenge?
A brief background
In the late 1960s, the inventors of drop on demand technology began looking at the physics of droplet ejection from nozzles.
The inner workings of early piezoelectric inkjet printheads were relatively simple. The key component was a ceramic actuator, which became taller and thinner when voltage was applied to it. This expansion pushed pressured ink in a chamber and forced a drop of it out from the nozzle. The actuator chamber had one ink inlet, with a straightforward flow of ink from the inlet to the nozzle. This is called an end-shooter printhead.
However, there are limitations to end-shooter printheads. As there is only one ink outlet (the firing nozzle), if there are any unwanted particles or air bubbles in the fluid, there is only one way for them to go—out through the nozzle. Consequently, blockages occur, which disrupt printing. The air bubbles and particles need to be removed by purging, which causes printer downtime and wastes ink, adding to production costs.
As a result, technologies were developed that could cope better, delivering improved jetting performance and printer uptime.
High flow-rate ink recirculation technology
A crucial development in printhead technology was the invention and introduction of a ‘side-shooter’ printhead where the nozzles are in the side of the channel rather than the end. The nozzles, therefore, fire perpendicular to the flow of the ink. This architecture enables true, designed-in high-flow ink recirculation (i.e. the capability to recirculate ink directly past the back of the nozzles at a very high flow rate). This unique method of ink recirculation carries any particles or trapped air bubbles away in the ink path, rather than out via the nozzles, which are continuously primed and kept free of blockages. This ensures jetting is highly reliable and the printhead is fully operational for the maximum length of time.
While ink recirculation is now commonplace in printheads, not all recirculation technologies are the same. Prospective purchasers are faced with a variety of different approaches to recirculation, as each printhead manufacturer has its own characteristics, advantages, and disadvantages. The appeal of designed-in recirculation architecture is it enables fluid movement through a channel even when not jetting, and the architecture is very simple and open, allowing the fluid to flow easily through the ink paths to the channels.
Some printheads offer recirculation, but not directly behind the back of the nozzle. As a result, the chamber directly behind the nozzle is dead space for particles to collect and ultimately block the nozzle path. These printheads also have a convoluted ink path, which means there are more dead spaces for particles to settle and impede the flow of fluid.
A notable benefit inkjet equipment manufacturers and users see with effective high flow-rate ink recirculation is maximized printer uptime, which helps reduce costs. There is also quick recovery of the printhead (for example, following mechanical shock from media crash), again minimizing downtime and maximizing efficiencies for users. These printheads require minimal maintenance and have low running costs as downtime and ink wastage are reduced. There are instant start-ups in the mornings because nozzles are constantly primed.
Designed-in, high-flow ink circulation also helps address some of the specific demands of printing, which digital technology had struggled to overcome. For example, it is important to ensure exceptional print quality, such as by printing smooth skin tones and small text while also printing high-opacity whites (for over-and under-white applications). Titanium dioxide pigments used to deliver the required opacity are prone to sedimentation, leading to blocked nozzles. This is prevented by the high ink flow rate of this type of circulation. Similarly, in glass printing applications, this technology ensures glass frit-based inks (durable, temperature-resistant inks composed of glass and ceramic particles) are kept in suspension. The technology further ensures temperature variation across the printhead is minimized, as heat is removed directly from within the actuator channels, virtually eliminating print density variations. It ensures colour uniformity across the print engine in wide, single-pass applications such as décor laminates. It is also possible to reliably jet highly pigmented, viscous inks, opening up many new applications for digital inkjet glass printing, such as architectural glass decoration.