Rules of attraction: An introduction to magnetic substrates
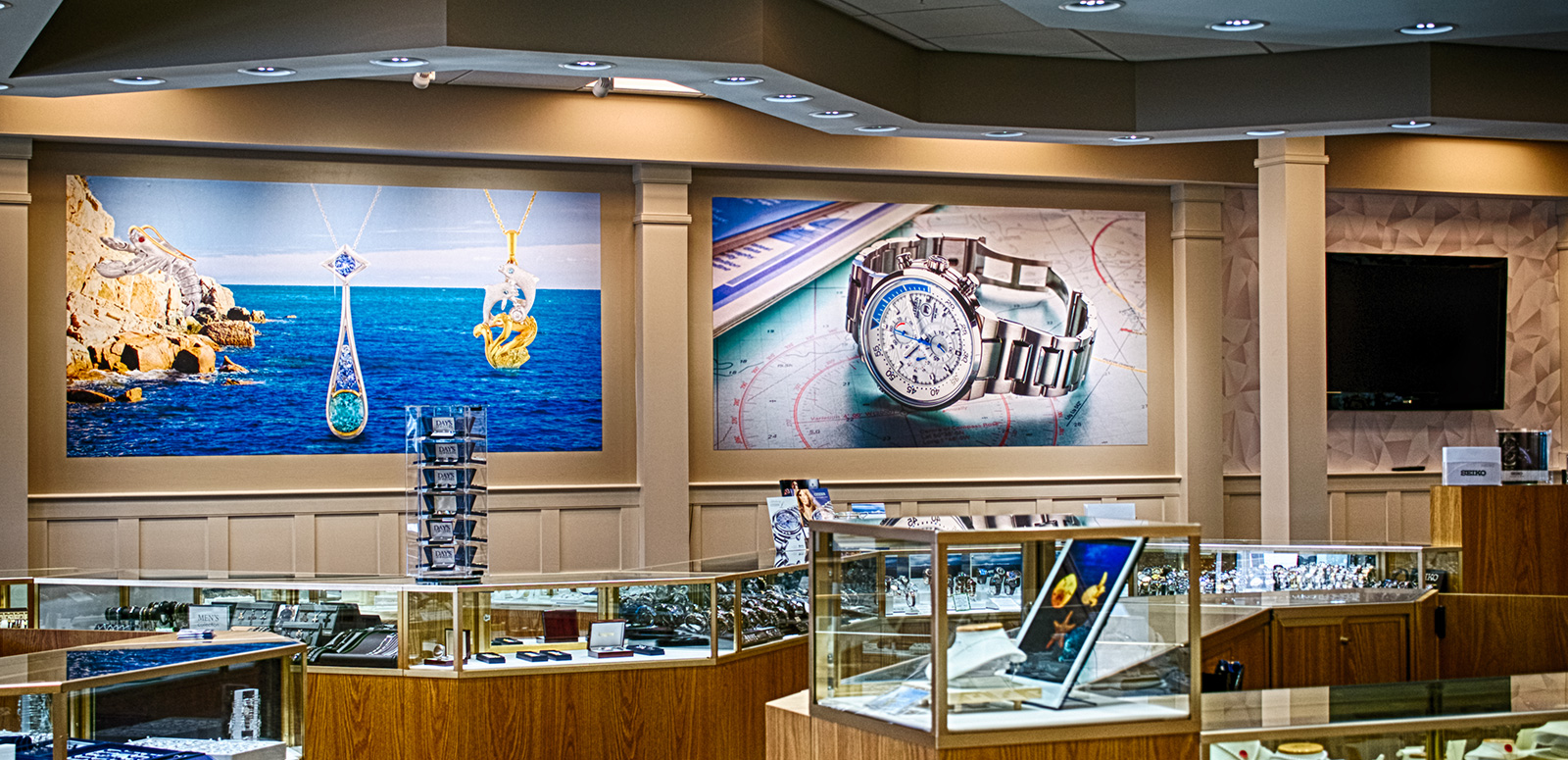
By Richard Romano
Those looking for a high-value print and/or sign application to offer customers, one that enables endless creativity and yet can simplify and expedite installation, especially that of retail graphics, should try magnetic materials.
The ability to apply printed graphics to a magnetic-backed material is nothing new, as perhaps a glance at one’s refrigerator will likely confirm. Small magnetic items have been used for novelty and promotional purposes for decades—think of a small bar magnet glued to the back of a calendar given out by a local bank or funeral home, or a small magnetic business card for the local dealership.
Today, magnetic sheets can be found at many office and business retailers that can be run through a standard desktop inkjet or laser printer. At the higher end, magnetic signs are ideal for buildings, vehicles, and other indoor and outdoor applications. At the even-higher end, magnetic materials can be used for wall décor and point-of-purchase (POP) displays, where graphics can be easily and quickly exchanged, perfect for fast-turnover retail spaces. Essentially, magnetic media and printing systems have become versatile enough to make magnets a high-value print application that goes far beyond the simple fridge magnet advertising your local pizza joint.
Printing on magnets, though, is not a trouble-free process, and a magnetic substrate offers new challenges in terms of image quality and colour management—in addition to the basic problem of getting a big magnet through a largely metallic printing press, especially at any kind of productive speed. However, advances in technology are creating new magnetic media applications for small-, wide-, and now super-wide-format printers and installers, with several emerging approaches to printing images on magnets.
Direct printing on magnetic substrates
The simplest way of printing on a magnetic substrate is…printing on a magnetic substrate. Basically, a sheet or roll of magnetic material is fed through a press or printer. However, where the trouble lies is when using a sheet-fed or roll-fed printer.
For one thing, magnetic sheets are thicker than many other types of media and, consequently, feeding problems can occur.
There is also the problem that printing equipment has lots of metallic parts which, logically, can be affected in various ways by running magnets over them. When running magnetic materials at high speed, it can inadvertently induce a magnetic field in a material—and one thing to avoid is magnetizing bits of your printer. There is also the potential for printer and printhead damage, which may invalidate its warranty and/or service plan. That’s why it is critical to choose magnetic material that’s suitable for, or even certified for, a particular type of press.
In addition to damage to the printer, there is also the potential for damage to the magnet. Laser imaging systems—those that use some variety of electrophotography—require high temperatures as part of the fixing process. Not all magnetic materials can withstand exposure to this heat, and can soften, deform, and even melt. So, choosing an appropriate magnetic substrate for a press is the key to avoiding a “meltdown.”
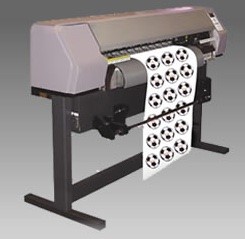
Printing via transfer sheets
Another way of getting images onto magnetic substrates involves using an intermediary material. You print—via offset, digital, or some other printing technology—onto a label, transfer sheet, or other material, and then apply it to the magnet, often using a pressure-sensitive adhesive or even dye-sublimation. This avoids all the mechanical issues involved with printing on magnetic substrates.
Print and magnetize solutions
Another solution to at least some of the challenges of running a magnetic material through a printer or press has been to use a material that is magnetized after printing. This is referred to as post-magnetized material. You print on it just like any thick plastic or vinyl substrate, then, as part of the finishing process, you run it through a magnetizing machine. Using post-magnetized material also helps solve one other related magnet problem: stacking. If you stack magnetic graphics, the sheets will stick together. This stickiness also affects feeding on the input side if you are printing on pre-magnetized material. Post-magnetized substrates are a good way of solving this problem.
However, this means you have an extra piece of equipment to buy: a magnetizer. A magnetizer can be a large industrial machine, a small handheld device, or anything in between. The most appropriate choice will depend on the volume of magnetic print work. For instance, an industrial-scale magnetizer is not needed for the occasional sign or refrigerator magnet, but for a substantial volume of magnetic work, it will be faster and more efficient to invest in a large-scale device, or even an inline solution.
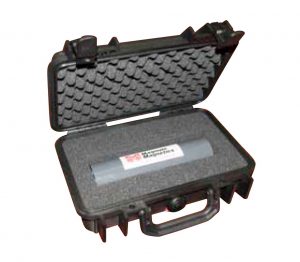
PPI
When searching for magnetic solutions, a term often encountered in the literature is “poles per inch” (PPI). As you may recall from high school physics, magnets are polarized; they have a north and south pole and it’s the attraction between opposite poles that makes a magnet magnetic. Poles per inch—which in these types of magnetic substrates ranges from a low of four to a high of around 16—refers to the number of north-south poles per linear inch. A higher PPI means a stronger “grip,” but the tradeoff is a lower “reach.” That is, a magnet with a high PPI will have a higher holding strength, but it will attract at a shorter distance. For example, with refrigerator magnets, some can hold up a thick postcard or a folded takeout menu without sliding down the front of the fridge, while others can barely hold a piece of paper. Likewise, some “grab” the surface from a few inches away, while others need to be right up close before they stick. These differences are essentially due to differences in PPI. It is also a function of the thickness of the magnetic sheet.
Other magnetic display options
There are several options to get an image on a magnet: direct printing on magnets, transfer sheets, and post-magnetized magnetic material. There are other options out there; one system involves printing graphics on magnetically receptive material rather than on the magnet itself. Flexible magnet sheets can be affixed over a wall or other surface using various adhesives. Then the finished graphics—printed not on a magnet, but on magnetically receptive material—are layered on top.
Companies that use this approach start with a layer of magnetic receptive paint, which is applied to a wall or other surface. This is a kind of primer that contains iron particles which make the surface magnetically receptive. Then, a magnetic sheet is applied on top of the primed wall, and the final display graphics stick to the magnetic sheet. Graphics can be swapped out, layered, and otherwise creatively arrayed to create highly modular designs.
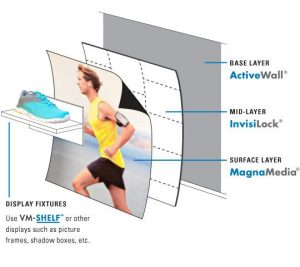
Ensuring press compatibility
As with just about any substrate for digital printing, for best results, the magnetic substrate needs to be compatible with the press. So, when working with a supplier, inquire as to whether it has been certified, or at least tested, for use on a given press. Running incompatible media can result in, at best, poor image quality and colour reproduction, or at worst, an inability to get the material to perform on-press—or even damage to the press and/or substrate.
Don’t forget finishing
As in traditional paper-based printing, especially wide-format or specialty printing, products are finished in some way—they are cut, folded, mounted, grommeted, etc. A lot of these will likely not apply to magnetic materials, but those finishing processes that do can also present similar issues with regard to feeding, stacking, and cutting, especially contour cutting. When using post-magnetized material, it can be more efficient to magnetize a large sheet rather than smaller-cut magnets, depending on the magnetizing system. In many cases, the output may need to be scored and pulled apart by hand—which can be a bottleneck when doing high-volume work.
Opportunities, benefits, and applications
Despite the challenges of productively working with magnets, there are opportunities in producing these kinds of products. Here is just a short list of the types of applications for magnetic media:
- Printed specialty objects
- Die-cut magnets
- Business cards
- Postcards
- Direct mail
- Labels
- Packaging
- Indoor/outdoor signage
- Restaurant menu boards
- Retail signage/graphics
- Vehicle graphics
- Interior wall décor
- Changeable POP/POS displays
And there are more. Ultimately, magnetic printing is a high-value application and is, in many ways, only limited by the imagination and creativity of the print provider and the print customer.
[BIO] Richard Romano is managing editor of WhatTheyThink, a media organization in the printing and publishing industry, offering a wide range of publications that deliver unbiased, real-time market intelligence, industry news, economic and trend analysis, peer-to-peer communication, and special reports on emerging technology and critical events.