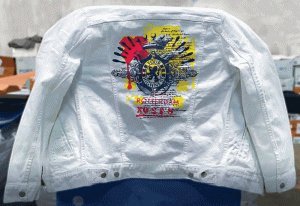
The direct-to-garment (DTG) market is moving beyond T-shirts, with custom printing on higher margin items such as jackets. Photos courtesy Roland DGA
By Kitt Jones
One of the most prominent changes in the print industry over the last few years has been the increased demand for direct-to-garment (DTG) printing. A large part of this change is due to a growing trend in customization and personalization, accompanied by the rise of e-commerce and “one-stop shops” offering customers a wide range of apparel resources.
In 2021, sales of DTG printing products reached US$202 million (C$253 million), despite the effects of the pandemic. Over the next 10 years, it is projected the global DTG printing market will see a compound annual growth rate (CAGR) of 8.3 per cent.1
Today’s print shop clients are often looking for specialty printed and short-run apparel along with their graphics, and DTG printers have emerged as a critical technology. Manufacturers are responding with new DTG printers offering increased flexibility and appeal as an in-house resource.
Managing demand
While customers are asking for more DTG products such as T-shirts, hats, and bags, many print shop owners have not been able to provide these services internally. To satisfy their clients’ requests, print service providers (PSPs) have been outsourcing their DTG production—which can constrain the shop’s ability to control quality, timing, and costs.
To address this need, printer manufacturers have developed innovative DTG printing technology, which is spearheading advances in related ink and pre-treatment options. These changes are making DTG printing workflows more accessible and flexible than ever. Today’s DTG printers are both powerful and versatile, providing the on-demand production capability needed to help PSPs fulfil custom and short-run orders in-house.
The evolution of DTG technology
In the last few years, owners of DTG printers have found ways to speed up production through a variety of pre-treating and heat pressing techniques. However, while this technology is becoming more powerful and less expensive, one-platen printer production can only go so fast.
Today’s improved inks and more comprehensive software are important for increasing the speed and efficiency of DTG printing. However, the real leap forward is coming from flexible print production, which allows companies to diversify their product line and set themselves apart from the competition.
Printer manufacturers have developed DTG print technology which provides faster, better production on a wider variety of materials and substrates. For example, Roland DG recently released a DTG printer featuring a 1346.2- x 1625.6-mm (53- x 64-in.) bed and a 203.2-mm (8-in.) Z axis, allowing users to print on multiple shirts at once, or on larger, more lucrative products such as towels, jeans, and blankets. The power and versality of these types of printers changes the economics of customized and short-run production, yielding higher profitability for print shop owners.