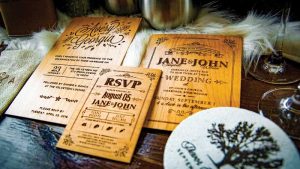
Carbon dioxide (CO2) engravers are capable of handling almost any material, from wood to acrylic, treated aluminum to glass, and well beyond. Photos courtesy Epilog Laser
By Mike Dean
When it comes to laser engraving, carbon dioxide (CO2) engravers are capable of handling almost any material, from wood to acrylic, treated aluminum to glass, and well beyond. However, how do you know what speed and power settings to use for different materials? It is a simple question with a not-so-simple answer.
Speed and power settings depend mainly on two things. The first is the material you are engraving or cutting, and the second is the wattage of the machine you are using. On materials such as wood, the higher the wattage, the faster you can set the speed to get to the same engraving depth as a lower-wattage laser. Therefore, the higher the wattage, the more throughput you can achieve from the same system. Materials such as acrylic require little power to engrave, so they can be marked almost as quickly with a low-wattage laser as they can with a high-wattage laser. The thickness of the material you are engraving or cutting will also impact the speed and power settings you select. For example, a 19-mm (0.75-in.) piece of acrylic will take more power to cut than a piece that is only 6.3 mm (0.25 in.) thick.
Below is a general overview of popular engraving materials, along with some helpful tips for how to produce the best possible results for each project.
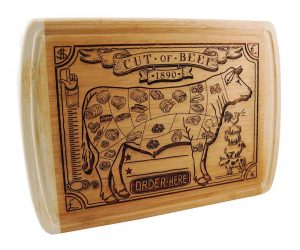
Wood can be engraved and cut very easily. Lighter-coloured varieties also produce a nice contrast where the laser burns away the wood.
Wood
Wood is by far the most laser-friendly material. It can be engraved and cut very easily, and lighter-coloured varieties—such as cherry or maple—produce a nice contrast where the laser burns away the wood.
Additionally, every type of wood has its own characteristics. Some are denser than others, with harder woods requiring more laser power to cut or engrave. The most common hardwoods used with the laser are cherry, walnut, maple, and alder. These woods have relatively few veins of grain running through them, while oak has medium to large veins. Since it is much grainier, oak is a less desirable choice for wood engraving, as designs vary greatly in height, and they also have a very non-uniform appearance.
Tips and techniques
- Wood is a great material to laser engrave because it discolours, and the depth of engraving is larger compared to most materials. The downside is it takes a lot of power to deeply engrave wood at high speeds.
- Most wood can be engraved using full power, whether you are using a 25-watt (W) laser or a 120-W laser.
- Depending on the wattage of your laser, the best approach is to set the power at 100 per cent and adjust the speed to obtain the desired depth.
- Wood is very simple to work with, and you can produce nice detail with as little as 300 dots per inch (DPI). Further, 600 DPI engraving produces even better results.
- Greyscale clipart images look superb when engraved into wood. Since the wood reacts differently to each level of grey, you can produce a remarkable amount of contrast.
- Engraving greyscale clipart images also creates a shading effect that is almost three-dimensional in appearance.
- Greyscale photographs can also look great, but these images usually need to be processed through specialty software before they are truly ready to be engraved into wood.
- Your results will turn out better if the grain of the material runs parallel with the X-stroke of the machine’s carriage.