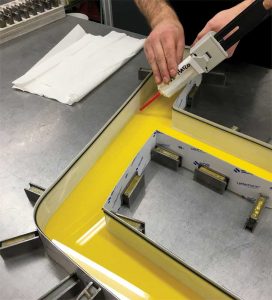
Signage is constantly exposed to ever-changing conditions and must be made with an adhesive flexible enough to keep up. Photos courtesy MPI Matco
By David Mucciarone
Signage is constantly exposed to ever-changing conditions. Therefore, it must be made with an adhesive that is flexible enough to keep up.
While durability and strength play important roles in the industry, they are only a fraction of the story. It is also crucial to consider how a sign’s environment can impact its esthetics, compliance, and visibility.
The adhesive is literally the glue that holds everything together. If it has strength, but not flexibility, it inevitably becomes the weakest link in the signage system. Imagine a bodybuilder attempting a routine on the parallel bars. It might sound cringeworthy, but this is the reality a sign could face if it is fabricated using the wrong adhesive.
Moving with the times
Signmakers understand the importance of adapting to market demands. They continuously optimize the effectiveness, capability, and relevance of their products.
Though common materials used for signage still include aluminum, acrylic, plastics, and galvanized metals, there are increasing expectations that have affected material selection. Greener, more environmentally friendly options have become deciding factors for many clients. Further, the rising costs of metals and aluminum have increased the demand for new, more lightweight signage materials, including aluminum composite material (ACM) panels. While these changes have dramatically reduced the thickness and cost of aluminum pieces, they have also increased the likelihood of damage to the signs made with these materials.
Lightweight signs are exposed to very different risks. These considerations are imperative when selecting an adhesive, as not all products are created equal. Knowing what types of adhesives work best with different materials will help reduce scraps, repairs, or costs in the long-term. Respecting quality standards is more than just esthetics. After all, well-made signage is all about form meeting function.
Mitigating wear and tear
Read-through and adhesive cracking are common problems seen in the sign industry, due to the materials typically used in signage applications.
Read-through occurs when there is distortion or visible marks on the substrate over a cured adhesive bond line. Adhesive cracking, also known as bond failure, is caused when the adhesive bond between the substrate and the sign face fails, causing the sign face to detach or fall off completely. This can result in damage to the sign and potentially create safety hazards.
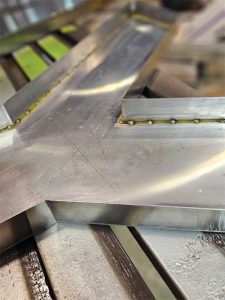
Knowing what types of adhesives work best with different materials will help reduce scraps, repairs, or costs in the long-term.
Signage that is lightweight and easy to handle is often made up of thin substrates, such as plastic sheets or aluminum composites. These materials each have their own thermal expansion coefficient, which means they can expand or contract significantly with temperature changes. This can create stress at the bond line between the substrate and the adhesive, leading to read-through or adhesive cracking, often characterized by deformations, visible marks, or distortion.
If the adhesive used in the sign application lacks the flexibility to accommodate the thermal expansion, the problem worsens, and the adhesive may crack or break, leading to further substrate deformation and read-through.
Adhesives formulated to minimize the occurrence of read-through and adhesive cracking challenges typically have a low modulus, high flexibility, and low shrinkage. This helps minimize the stress and distortion of the substrates over the cured adhesive bond line during thermal expansion and contraction. These adhesives also have a low curing temperature, which is important for preventing thermal distortion of thin substrates, composites, and plastics.
By choosing the right adhesive for the job, signmakers can ensure their bonds are strong, durable, and long-lasting.