Cutting through the noise
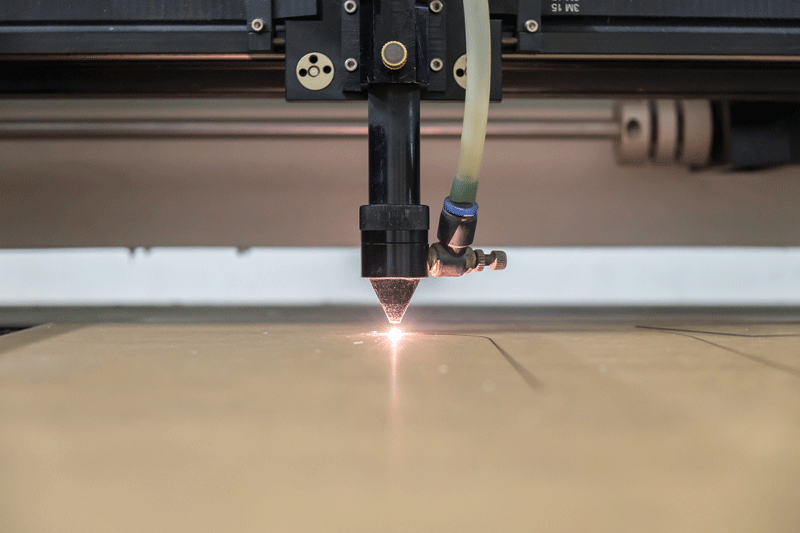
By Carly McHugh
When it comes to delivering sharp, eye-catching sign projects, one of the top priorities is making sure you have the right tools. This helps guarantee your shop’s fabrication team can achieve the desired effect for
each job.
The rise of architectural and dimensional signage has allowed shops to get even more creative with their equipment, utilizing laser cutters/engravers and computer numerical control (CNC) routers in more inventive ways to produce signs that (quite literally) stand out to customers and passersby.
However, for those just starting out or looking to explore a new avenue for their business, it can be challenging to decide which machine is best for their needs. Some shops may already have one or both of them on hand but are unaware of how to maximize on their capabilities.
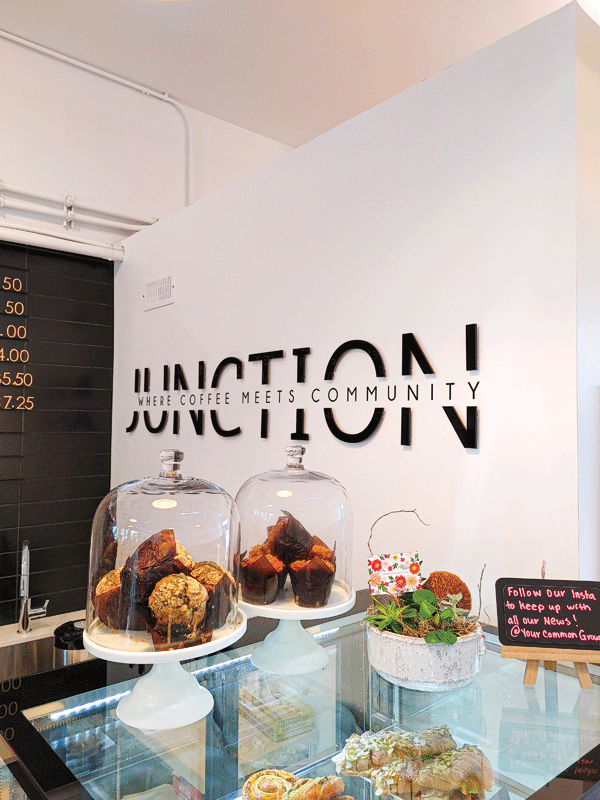
For a more detailed analysis of the untapped potential of lasers and CNC routers, we spoke with Clayton Letourneau of Custom Sign Lab. With expertise in using both machines for sign fabrication, he provided further insights into their similarities and differences, their range of capabilities, and how shops can leverage their skillsets to create outstanding, cutting-edge signage.
Sign Media Canada (SMC): How does the precision of lasers compare to CNC routers when producing intricate signage designs?
Clayton Letourneau (CL): From our experience, the diameter of the cut with a laser is typically less than 0.7 mm (0.03 in.), and with a CNC, we tend not to make cuts with tooling smaller than 2.5 mm (0.1 in.). Therefore, there’s a dramatic difference in precision, along with the size of letters or shapes you can cut.
However, the larger factor when it comes to the precision between the two devices is they’re both reductive processes. One removes material with a tool, while the other removes it using heat. With a laser, the removed material turns into vapour. With a CNC, it turns into particulate. This leads to a very different finished product and a very different viability of the size you can work with.
With our laser, we can cut characters as small as 7.6 mm (0.3 in.) high. We couldn’t do that on a CNC, because the vacuum dust collection system would pull those letters right up and through it. Typically, anytime we get down to a letter smaller than 76.2 mm (3 in.), we just put it onto the laser. It’s so much more practical and quicker for smaller, finer details.
SMC: What are the differences in operating costs for each machine, considering factors such as maintenance, energy consumption, and consumables?
CL: The largest difference in our setup is the fact one uses a dust collection system and the other uses a fume extractor. The laser runs in the range of 1,600 to 2,000 watts per hour. We use an 80-watt carbon dioxide (CO2) laser, but after you factor in the stepper motors, the chiller, the fume extractor, the computer drivers, and all of the other components, it adds up to about the consumption level of a hairdryer. The CNC probably doubles it, but neither are dramatically high compared to the potential for revenue. For the CNC, we have a 3.7-kW (5-hp) dust extractor and a 2.2-kW (3-hp) router, so it’s going to run a higher cost to operate. However, when you weigh this against the potential revenue from having the machines, it’s pretty nominal, in terms of operational costs.
SMC: What are the advantages and disadvantages of using CNC routers and laser machines for creating dimensional signage?
CL: The CNC definitely has the upper hand for greater dimensionality, simply because you have more depth to work with. Our laser is more than a decade old; however, it’s maintained and in good working order. We typically don’t cut anything thicker than 17.7 mm (0.7 in.) on it. To switch over to cut under 12.7 mm (0.5 in.) is one lens, and more than 12.7 mm up to 17.7 mm is another lens, and you cut in multiple passes. However, it does have a bit of a height limitation, so you’re more restricted on what you can cut with the laser, despite the fact it has greater precision. With our CNC, we can easily cut objects up to 101.6 to 127 mm (4 or 5 in.) thick, because it has a higher gantry height, which is only dependent on the tooling height you purchase for the machine. Therefore, there’s a distinct advantage with the CNC for cutting larger dimensional lettering. You can build compound shapes really easily.
There’s also separation between the two machines in the type of materials you can use. A CO2 laser is a practical solution for cutting wood and acrylics. You can’t cut polycarbonate, simply because of the water content in the product. It creates an awfully nasty gas when you cut it, and it doesn’t give you a very good cut. The CNC can cut wood, sign foam, acrylic, aluminum, and die bond. We’ve even cut brass on our machine. Thus, there’s a larger variety of materials you can cut with the CNC. It just depends how much mess you want to deal with.
SMC: How do the cutting speeds of the machines compare to each other, and what impact does this have on production time and efficiency for projects?
CL: We’re a little bit conservative with our cutting speeds, although with the CNC, there are guidelines you have to adhere to for the best possible fidelity of the edges. Plus, you have to be conscious of the chip load of the tooling you’re using. This is essentially the rate at which you can evacuate the material you remove. If you’re moving too fast, at too great of a depth, you can break bits, and have really raw edges and poor cutting quality. If you move too slow, the same thing can happen. You have to follow the manufacturer’s guidelines for speed.
With the laser, it’s a similar relationship, but even if you operate at a slow speed, the only thing you need to worry about is reigniting the gas burned off in the process. We don’t use any inert gases when we’re cutting. We just use an air compressor to push the gas out of the way, which is then drawn out by the fume extractor. However, if the laser is moving too slow, it can reignite the gas and cause little flame flare-ups inside the machine.
Both machines cut at a similar speed. We typically run our CNC at 1,778 mm (70 in.) per minute, and our laser at about 1,524 mm (60 in.) per minute. They both penetrate about the same depth per pass, within maybe 2.5 mm of one another.
The big advantage in production speed is with the laser because there’s no debris post-cut. Therefore, there’s very little cleanup. Additionally, you don’t need to clamp it down. Everything is just held in by gravity. There also doesn’t need to be a vacuum bed. It’s much easier to take a small piece of material, put it on the bed of the laser, and move quickly through cutting some letters, whereas there’s a little bit more setup on the front and back end with the CNC. Per job, there’s probably a 10- to 20-minute advantage with using the laser.
SMC: What are the key considerations in terms of safety and environmental impact when choosing CNC routers and laser machines?
CL: The main environmental concern with the CNC is dust and particulate extraction. You’re going to need some type of setup that effectively draws the removed material away from the blade and out of the atmosphere. If you don’t have a proper dust and debris collection system, you’re going to end up with a really messy shop that has to be cleaned frequently. You’re going to have a hard time maintaining other operations, and your staff is going to have to wear particulate respirators. That’s a consideration, but you don’t need any exterior venting for it.
With the CO2 laser, exterior venting is an absolute must. We have a high-cubic-feet-per-minute (CFM) fume extractor that draws air out of the chamber of the laser, directly through a charcoal filter, and then out into the atmosphere. We use a charcoal filter simply because there are some less savoury fumes that can be drawn out, so the filter makes it a bit more environmentally friendly.
Further, neither of the machines should be unmanned, but there’s a higher possibility of fire with the CO2 laser, so you have to make sure you have an extinguisher ready and the materials you’re cutting are naturally combustible. Part of the process of using the laser is combusting your way through the material, as opposed to pushing a tool through it, so that’s something else to consider.
SMC: Can lasers provide unique advantages in terms of workflow, flexibility, or customization capabilities that CNC routers may not offer?
CL: The level of detail, engraving, and cutting for a laser is going to give a distinct advantage. It pairs really well with a flatbed ultraviolet (UV) printer. Utilizing a combination of contour cutting and engraving on a laser makes for some really interesting effects, and you have the ability to create some dimensionality through the material you’re using. For example, if you wanted to make a painted-back wayfinding sign with braille and raised lettering on the face, and a unique shape that’s something other than a rectangle, you could do your paint on the back, your print on the front, and then put it into a jig and perfectly cut out the shape in the laser. You have a way higher chance of damaging the finish by trying to attempt the same process with a CNC.
SMC: Do you have anything else you would like to add regarding the capabilities of laser machines and CNC routers when it comes to crafting sharp, attractive sign projects?
CL: Pairing a CNC or a laser with a creative operator is really going to be the advantage you’re looking for. With either machine, you have the opportunity to produce some really dynamic sign projects, if you think outside of the box.
The CNC has a number of different tooling setups you can utilize to capture dramatic, dynamic special effects, and depending on the program you use to output your files, you can do some really creative carving. You can work at a larger scale for height and depth, and you can also layer materials. If you’re using sign foam, you can do multiple slices of a shape and build a full 3D object much easier than you can with a laser.
The laser has the advantage of speed, quick prototyping, and fine details, and it works really well with acrylic. Everything you cut is pre-polished, so you already have a finished edge. There’s a huge advantage there from a production standpoint, and the best way to be creative with the laser is the choice of materials.
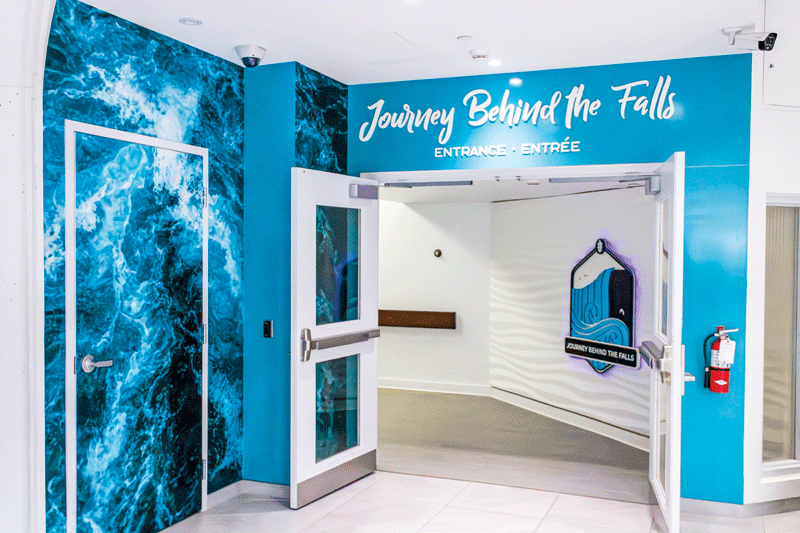
They’re both really great tools to have and they work well in tandem. There are also similar applications for the two machines, as well as dramatically different ones, so there’s no clear advantage between one or the other. It really depends on the core of your business. If you’re a graphics shop, or you do a ton of wayfinding, fine lettering, engraving, or branding, the laser makes more sense. If you’re a sign shop that does a lot of dimensional letters, dimensional signage, 3D signage, or traditional foam-based signage, or you’re using high-density urethane (HDU), the CNC tends to be a bigger asset. Our shop falls into both categories. We have a graphics division and a signage division, and both machines definitely help us out in production. However, even in our shop, the CNC gets used about three times as much as the laser. It just happens to be what works for us. There’s no clear winner or loser in which one is better.
Ultimately, it comes down to the creativity of your designer and your operator, as well as how you can understand the materials you’re working with and the relationship they have with each machine.