-
A competent vacuum hold-down system
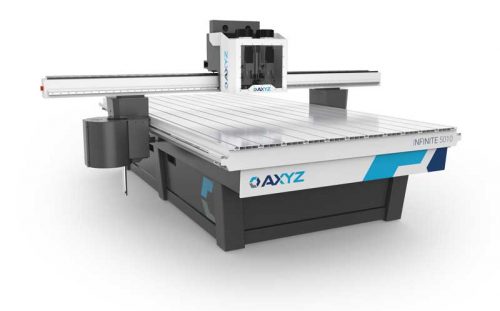
To produce a smooth, polished cut and stay competitive in the demanding signage industry, a computer numerical control (CNC) machine is well worth the investment.
The vacuum hold down ensures material stays in the correct place throughout the cutting process. Even the slightest material movement can put the software program, spindle, and material out of sync, invariably ruining the piece completely.
Selecting the right tools
Choosing the right tools and accessories will have a huge impact on the quality of the edge, and the overall look of the POP display.
When choosing collets and router bits, signmakers should keep the following tips in mind:
Collets
-
Choose the right type of collet to fit the spindle
Collets come in all shapes and sizes; therefore, it is important to buy one that best suits the CNC machine to avoid ending up with poor edge quality. Using the wrong one can also damage the spindle, machine bed, and the collet itself.
-
The collets should be changed regularly
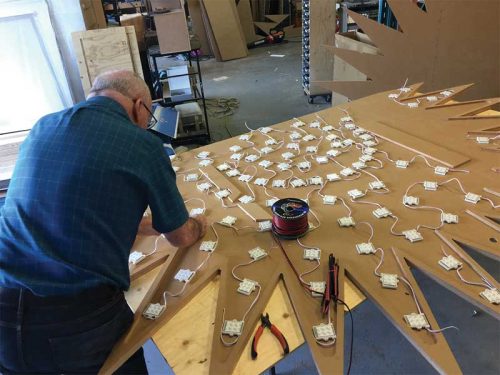
A technician from POP49 installs lights on a display that was cut on a computer numerical control (CNC) machine.
After three to six months of use, collets will no longer hold a router bit as straight and true as when they were new. Therefore, changing them regularly will help to prolong tool life. When inspecting a collet, metallic damage, such as bell mouthing or burrs, should be checked with every tool change.
If damage is visible, the collet should be discarded and replaced. This ensures operations run consistently, good cut quality is maintained, and the life of the cutting tools is prolonged.
-
Match the collet shank with the tool shank diameter
Manufacturers often quote sizes in metric and imperial; therefore, it is important to read the data correctly to avoid mistakes. One common mistake is trying to fit a 6-mm (0.23-in.) shank tool into a 6.35-mm (0.25-in.) collet. It will go in and it can be tightened, but since it is not the right fit, it will put stress on the collet.
Router bits
-
Determine what type of flute is needed
There is an enormous choice of CNC router tooling available (e.g. single, twin, or triple flute) and all factors (material, density, etc.) need to be considered carefully. Selecting the right tool for the job can make the difference between a perfectly smooth and clean cut, or something that looks like it has been hacked out with a saw. If one is not sure what tooling to use they should contact a CNC expert for guidance.
-
Understand the difference between spiral bits
If one wants the bottom side of a part to look polished an ‘upcut’ spiral bit should be used. If it is the top side, a ‘downcut’ spiral bit is needed. Other points to consider involve effective chip extraction and how thick the material is. The ‘upcut’ spiral bit is better at cutting thicker materials and has the best chip extraction rate, while the ‘downcut’ spiral bit is best used for materials that are 3.17 mm (0.125 in.) or thinner. However, due to the reduced cutting speed required when using ‘downcut’ spiral bits, they are less effective with chip extraction.