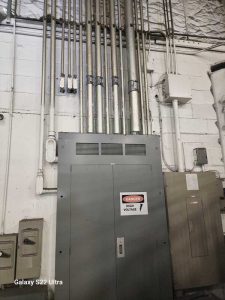
For wall installations, it is important for the team to evaluate what may be present on the other side, as interior hydro conduits may have a high voltage.
SMC: How do you adapt your installation approach based on factors such as weather, temperature, and exposure to elements?
JL: You really need to address it with the client first, and tell them, “You have water damage here. Your building is deteriorating here. It may not be the best idea to install a sign. You may want to have this looked at by a contractor. Maybe we could add some support on the backside of the building?”
This is called a through-wall installation. The installer will add ribbing on the internal part of the building to support the weight and the wind load, because, in the end, it comes down to liability. My theory is the last person who touched the building is responsible. Thus, even if we do take the chance, the owner says put it up anyway, and the sign falls down, they may come after us, because there’s no paperwork to back up the decision. The installer would need to sign a disclaimer saying the owner gave them permission to install the sign, even though they knew the condition of the wall. From a legal standpoint, you have to make sure you’re covered.
As an installer, we’re subcontractors for a lot of sign companies. Therefore, if the drawings show a certain depth and size of concrete footing, rebar cages and structures below grade, and the size of the anchors, you really have to follow those drawings to a tee, because they are approved drawings. If you deviate and go on your own judgment, and change the depth and the size, and something happens, you’re fully responsible for that call. It’s important to follow permit drawings approved by the city or township, or stamped engineered drawings to the letter, because then everyone’s covered from a liability standpoint if any part of the project was to fail.
SMC: How do installation methods contribute to the long-term durability of sign projects?
JL: When you’re installing a sign, it essentially becomes a part of the building. You have to ensure that in 15 or 20 years, it’s still going to be safely installed on the wall. Therefore, you really need to dot your i’s and cross your t’s, and make sure that after the sign is installed, you caulk the edges, and no water gets behind brackets or behind signage to cause damage to the building. Ultimately, there are a lot of steps to make sure it’s a long-term installation.
SMC: Can you share an example of a challenging sign installation you’ve worked on? How did you address any safety concerns and/or structural considerations?
JL: We installed a sign on a building in Windsor, Ont., which was probably close to 100 years old. The owner was adamant that we install the sign. It was very challenging, because it was on a roof, so we had to get scaffolding set up. The installation was done partially with a crane and partially with the scaffolding.
Then, about five years after the original installation, the building was starting to fall apart. It was a perfect example of a project where the owner said, “It’s my building. I understand the risks and possibilities of water damage and everything, but just install it.”
At a later date, he decided to restore the building properly, because it is a bit of a historical landmark in the city. They had us take the sign down, they did the proper repairs, and then we reinstalled it in the same location. This was a prime example of a building that was already damaged to begin with, but adding a sign to it did not help.