For a smaller sign shop, an MCR may include an assembly of photos taken during production, copies of electrical component invoices, a list of parts used and some related notes. For a larger manufacturer, a work order and shop drawing should suffice, if all of the parts are identified. If unsure, it is always a good idea to take production photos and attach them to the MCR.
When constructing a ‘family’ of like signs, one drawing can be identified and then referenced for all of the other signs.
The construction review should cover the following:
- Frame and enclosure.
- Ventilation openings.
- Sign face and/or panels.
- Moisture resistance and drain holes.
- Grounding and bonding.
- Electrical and thermal spacing.
- Wire routing and support.
- General workmanship (i.e. shaving, sharp edges and de-burring).
- Correct hardware.
- Electrical and supply conductors.
- Installation instructions with the sign.
- Included list of correct components.
There should also be a performance review of the following:
- Mechanical integrity.
- Exclusion of water.
- Strain relief.
- Grounding continuity.
Reorganization and changes
As mentioned, the 15th edition of UL 48 is has also come into effect as an ANSI standard. The document underwent STP review and voting. The most recent review, completed shortly before the October 2012 effective date, focused on a few sections that had been previously overlooked in the review process, including screws, metal thickness, water testing and some wire size requirements.
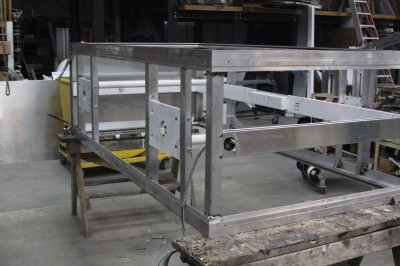
Each sign now requires a list or inventory of products used during its fabrication in the sign shop.
In addition to the ID number, each sign now requires a list or inventory of products used in its manufacture, the type of construction and the final installation location. Some of the other notable changes from UL include requirements for certified equipment, including tape measures, calipers, weights and electrical test equipment.
Also as mentioned, the new standard is a reorganization of the old one, with basically the same technical requirements, but with a new layout of information. The changes are based on the bi-national format, with information arranged in sections based on the different departments within a sign manufacturing facility.
Working alongside UL staff, the STP did not simply cut and paste these sections, but instead performed a complete review of newly added technologies, compliance with the National Electric Code (NEC) and new definitions required for clarity. The changes have been made to help ensure safer products and to support different levels of certification based on sign shops’ needs, while still allowing current forms and documentation to continue to be used.
Randall K. Wright operates RKW Consulting, which specializes in neon sign fire prevention, and represents the United States Sign Council (USSC) on UL’s sign industry business panel. For more information, visit www.rkw-consulting.com.