The world of UV printing technology today offers media and application versatility for a range of needs
By Ginny Mumm
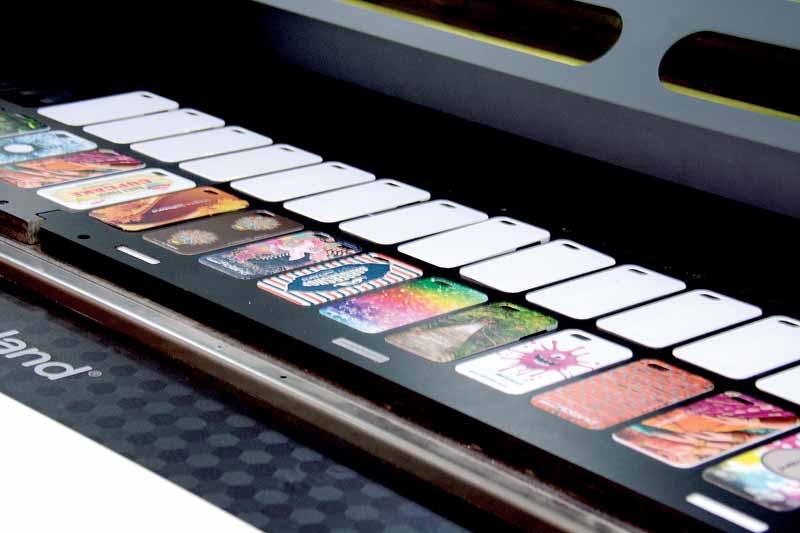
With today’s wider colour gamut and sophisticated print software, UV printers can create vibrant and intricate designs. Photos courtesy Roland DGA
As the global market for ultra-violet (UV) printing continues to grow, printer manufacturers are responding with innovative and versatile solutions for print service providers (PSPs). Advances in printer technology along with expanded and improved inksets, accessories, and updated raster imaging processor (RIP) software have made the latest UV printers more accurate, productive, and flexible than ever before. In addition to allowing users to print on just about anything, these printers can now produce vibrant, high-quality output rivaling output from other production devices.
To better understand the trends and innovations in UV print production, we talked with Jay Roberts, Roland DGA product manager for UV printers, who spoke about the ways the latest UV printing technology addresses today’s market.
Why are PSPs interested in UV print production? What makes this technology impactful?
Jay Roberts (JR): With its ability to print on a wide variety of substrates and 3D objects, UV printing offers exceptional media and application versatility. Users can personalize and customize materials and objects in a range of sizes, allowing PSPs to upsell existing customers and appeal to new ones. UV printing capability also opens opportunities to enter new markets, including packaging, promotional products, point-of-purchase displays, art, and interior design.
In addition, UV printing offers users a simple and straightforward production cycle. Since UV inks print directly to the end substrate, users avoid the need to print, laminate, and then mount their graphics, saving time and streamlining workflows.
How have inks evolved?
JR: The evolution in UV inks has been a key element in the increasing popularity of UV printers. Today’s UV inksets offer users a widened colour gamut, which creates a larger colour space for printers to match brand colours or hit the perfect hue for their clients. These advanced inksets yield high-quality output comparable to the output from eco-solvent printers and allow easy cross-platform production.
Specialized inksets are also being created to respond to users’ differing production needs. In addition, users can transition from one inkset to the other as their production needs change over time. Another innovation in UV inksets is the widened number of configuration options now available. Some inksets offer users as many as seven different ink configurations to meet their specific needs.
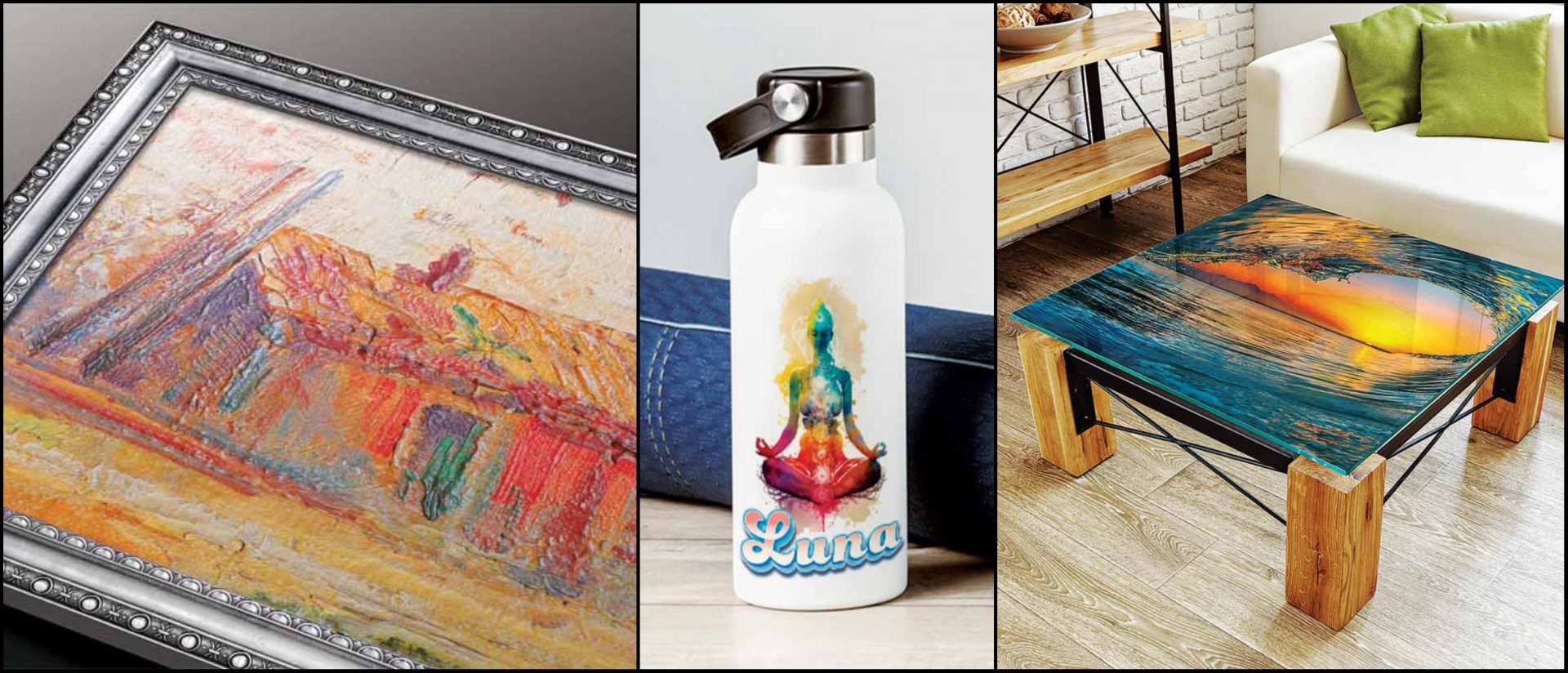
Newer UV printers have features optimizing printing on curved surfaces, along with attachments that make it easy to print directly on cylindrical objects.
How does having UV print capability help print providers capitalize on trends?
JR: Customization and personalization are only increasing as businesses seize the potential these services provide for additional profit and connection to their clients. Print shops can offer these services on products they already provide, such as signage, or expand their offerings to include printing on products like promotional items, golf balls, and phone cases. UV printing helps PSPs meet all these needs with quick-drying, durable, and scratch-resistant prints.
Another advantage of UV printing is its white and gloss ink capabilities. Adding contrast with a base layer of white ink or effects with gloss ink enhances the look of the product. Additionally, users can add spot colour and a matte or gloss finish to set their designs apart from the competition. UV prints can also be layered to create a texture simulating popular embossing or three-dimensional effects.
What about hybrid printers? What benefits do they provide?
JR: Hybrid UV printers offer the ability to print on rigid materials such as board stock and metals, as well as printing roll-to-roll media for graphics and backlit displays. Hybrid UV printers are also being used for printing on heavier textile roll-to-roll media used to create products such as umbrellas and awnings.
In addition to offering more versatility for customers, hybrid printers have a reduced footprint compared with traditional flatbed printers. Over the past few years, printer manufacturers have begun offering a range of bed sizes to accommodate the needs of users, from deeper and larger beds to more compact options.
Customizing objects continues to be popular. What are manufacturers offering to make this process easier?
JR: Along with other production enhancements, the newest UV printers can accommodate objects of greater thickness, thus increasing the range of products that can be printed on. Many flatbed or hybrid UV printers can print on objects up to 177.8 mm (7 in.) thick or more.
Printing on curved or uneven materials can be challenging due to the materials’ varying distance from the printheads. However, newer printers offer a “distance mode” allowing detailed prints on these materials without any loss in quality.
Are there accessories facilitating printing on 3D objects?
JR: Modern UV printer accessories offer users increased capabilities and the opportunity to broaden their product range to include popular products such as water bottles and tumblers.
Users can also print on the entire circumference of cylindrical objects such as insulated water bottles, glass vases, candles, and other objects of various sizes and diameters This additional printing capability with no loss in quality is a win-win for PSPs and their clients.
What have the latest software improvements brought to UV printing?
JR: The evolution of RIP software has kept pace with ink and printer technology advancements. The newest RIP programs come with a wide range of features and modes to help users produce more accurate output, more rapidly.
While colour management used to be a key concern in digital printing, recent RIP software provides profiles and modes that manage colour extremely well. Users can still create their own colour profiles, but typically find they no longer need to. Today’s printer software can also measure the colour in a swatch or paint chip, and reproduce it with remarkable accuracy.
Roland DG printers, for example, come with the VersaWorks RIP software included. VersaWorks offers advanced features third-party RIPs cannot provide. One feature helping users create special effects is the ability to control UV lamp intensities. This control can be used for special effects including a foil technique, where a user lays down a spot of uncured gloss ink, adds foil, rubs it in, and cures it, leaving the foil in the print. Although these special techniques can be more labour-intensive, they add impact and value to art or decor projects.
What do you see for the future of UV printing?
JR: In the next few years, I anticipate there will be many announcements about new UV printer platforms offering increased speed and production capabilities. Manufacturers are listening and responding to the market’s demand for additional speed and for continued advances in vibrant, accurate production.
Ginny Mumm is a freelance consultant for digital inkjet printer/cutter provider Roland DGA. For more information, visit www.rolanddga.com.