Acrylic Face Mounting: How to make a print really stand out
By Steve Yarbrough
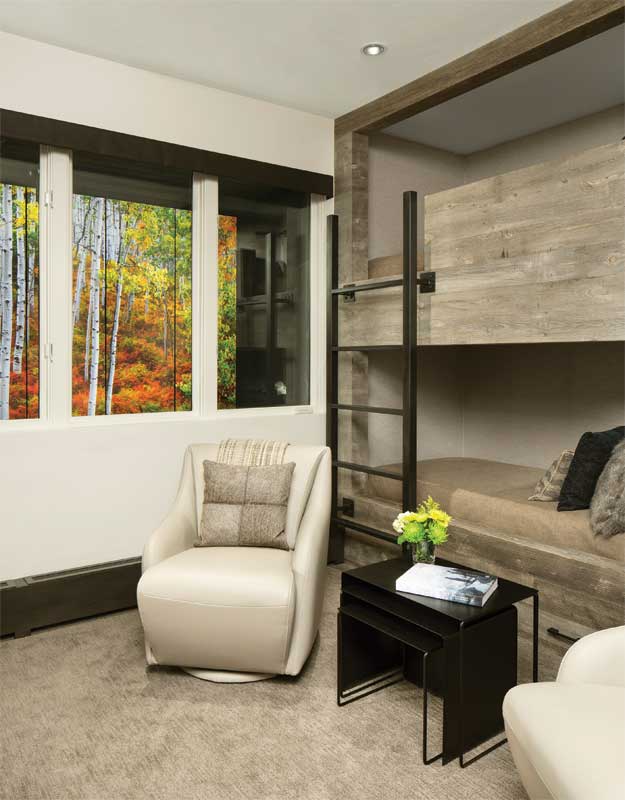
Acrylic face mounting can make a print really stand out, which is an essential prerequisite for fine art and other high-end applications. In order to produce a visually appealing output, there are five physical material aspects one must consider.
-
Photo paper or print media
The photo paper or print media plays an important role in the acrylic face-mounting process. One must always use good quality paper for an acrylic print. The most popular print media—and the one which the author prefers for most projects—is metallic paper. Whether it is satin or glossy, metallic paper enhances the vibrancy of a photograph. Not all pictures require metallic paper though; portraits, for example, often produce the best results on a pearl-finish type paper. Every surface has a roughness average (RA) and, the smoother the surface of the photograph, the better the results will be during the face-mounting process. If one does not have a completely smooth surface, they risk getting tiny air bubbles in the print called silvering.
-
Acrylic
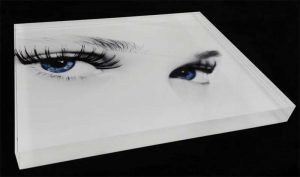
Another important aspect for face mounting is the acrylic itself. Not all acrylic is alike: there is cell cast acrylic and extruded acrylic. Cell cast acrylic is harder, has a more uniform thickness, is more scratch-resistant, and is typically clearer than extruded acrylic. Most people in the signmaking industry only use cell cast acrylic for face mounting, regardless of its thickness. There can be slight variance in thickness when dealing with this material; therefore, a laminator that can adapt to these variances definitely helps.
Heat can be used to shape acrylic into a variety of items such as furniture or art pieces. The material is also affected by humidity, which can cause the acrylic to warp, even after face mounting. In such a case, for example, the acrylic starts flat and is fine until after a period of time, when environmental conditions begin to cause damage. Warping is caused by differential moisture absorption on the face of the acrylic versus the back surface, which is covered by the print and, in some cases, a non-acrylic backer and cleat-style hanging. This issue can be resolved by using another piece of acrylic as the backer instead of some other material; however, this would result in a more even reaction to moisture absorption on each side of the mounted print. Similarly, it would create a more even reaction to thermal changes if it were part of the cause.
Acrylic can turn out to be an expensive material.
A single 2438- x 1219-x 19.5-mm (96- x 48-x 0.75-in.) sheet of museum-quality acrylic can cost nearly $4000. While this acrylic type is not required for most projects, one cannot expect to see stunning results with cheap material from a local store. However, cheap acrylic is good to practice with and hone one’s mounting and polishing skills.