More than just putting up a sign
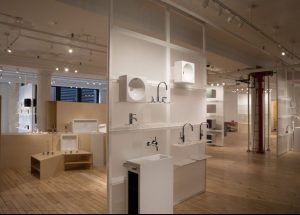
The most versatile acrylic with the broadest range of uses is continuous cast. It is strong and lightweight, with good optical clarity and substantial craze resistance. Further, it is available in larger sizes, whereas cell cast is limited by the size of the glass used to make it. Continuous cast is an excellent choice for point-of-purchase displays, interior and exterior signs, skylights, and countless other retail applications. It works well with back and edge lighting, including LED lights, because of its light transmission and diffusion properties. It is also worth noting clear, continuous cast acrylic is approved by the U.S. Food and Drug Administration (FDA) for food contact.2 Thus, it is a strong option for use in grocery store produce displays, food bins, and countertops.
Extruded acrylic is flexible, suitable for bending and fabricating, and available in large sizes. However, it lacks the pristine optical clarity of cell cast or continuous cast acrylic and is susceptible to crazing when not cleaned properly. Continuous cast and extruded acrylic are sensible choices for point-of-purchase displays that are changed and updated frequently—for example, end-cap displays in a retail store or displays commonly seen in convenience stores. Additionally, cell cast and continuous cast have a higher resistance to chemical attack due to their higher molecular weight, while extruded acrylic is a softer material.
Impact-modified extruded acrylic is optically clear and delivers fabrication flexibility, with superior impact resistance compared to cell or continuous cast. This sheet product is appropriate for some of the same applications as polycarbonate. However, the two materials are not the same and have some notably different performance characteristics.
Both acrylic and polycarbonate are classified as thermoplastics—a plastic material that becomes pliable above a specific temperature, then solidifies when it cools. Which plastic a sign shop selects depends on a few factors, including the application, sign type, and what is specified for the project.
The challenge lies in addressing the needs of a given sign project while still providing the best value for the customer. For example, acrylic has the highest gloss of any thermoplastic. For signs requiring high gloss and forming letters or images, acrylic is somewhat better than polycarbonate.
Polycarbonate sheet is a more robust material than acrylic and is considered virtually unbreakable. Relative to acrylic, polycarbonate offers greater heat resistance, higher impact strength, enhanced ultraviolet (UV) resistance, and increased resistance to breakage. Additionally, there are numerous other considerations to review before choosing a substrate.