More than just putting up a sign
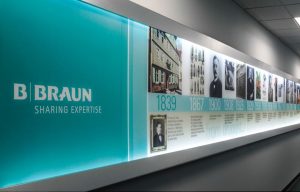
By Jane Nash
As the world begins to emerge from the COVID-19 pandemic, the trillions of dollars of stimulus money pumped into the economy are driving an unprecedented surge in retail spending. The National Retail Federation (NRF) projects some $4.33 trillion in spending in 2021, much of which is predicted to be in-store, as a public weary of staying home seeks out once-familiar shopping experiences.1
To meet the rush, retailers have invested heavily in features to attract shoppers and enhance the shopping experience. Most of the attention has centred on technology innovation and adoption, but the customer experience is about more than click-through rates and leveraging smartphone capabilities.
Technology is one piece of the in-store customer experience, but another significant part is walking through a store and browsing. One of the most critical aspects of curating a positive in-store experience is choosing the right thermoplastic sign to draw customers in and, when inside, guide them with noticeable point-of-purchase and product displays.
Polycarbonate or acrylic?
The first step is to choose the best sign material for the project at hand. Before selecting what type of panels to use or debating between light-emitting diodes (LEDs) or fluorescent bulbs, one should choose the substrate that works best for the business’s sign. When it comes to lighted sign panels, the choice is between a polycarbonate and a high-impact acrylic (also called impact-modified acrylic [IMA]). The more information retailers have about each option, the better able they are to make qualified, informed decisions.
Sign-grade acrylic is impact resistant, durable, versatile, flexible, and suitable for cutting, bending, drilling, and gluing. All these features make it an excellent choice for evolving retail environments. There are different types of acrylics with various characteristics able to meet the needs of specific applications.
Cast sheet is manufactured using a method known as the cell cast process, while extruded sheet is manufactured using a process known as continuous manufacturing. In the cell cast process, a casting liquid is poured between two plates (usually glass), which have a gasket between them to form a cell or contain the casting liquid. Then, the resin solidifies, usually through polymerization or crosslinking.
Cell cast acrylic sheet has excellent optical qualities and resists crazing (tiny cracks that can form on the surface of some thermoplastics). This makes it a popular choice for cosmetics counters because the chemicals in perfumes, colognes, and lotions can find their way into cracks and degrade surfaces over time. Cell cast delivers an elegant look, accentuating the value of premium products such as jewellery and cosmetics.
Continuous casting is a production form for manufacturing acrylic sheet. The process involves pouring partially polymerized acrylic between two highly polished stainless steel belts.