Adding logos to ice sculptures

He participated in ice-carving demonstrations and competitions. His work showed up everywhere from the 1988 Winter Olympic Games in Calgary to Winterlude in Ottawa to the Ice Magic competition in Lake Louise, Alta.
Finally, after 30 years as a chef, he left the culinary profession in spring 2007 to devote his full time to Fire and Ice. Since then, the company has produced work for weddings, corporate functions, baby showers, holidays and many other events. It has compiled an impressive list of achievements, including sculptures for the Juno Awards, which were hosted in Saskatoon in 2007, as well as an ice replica of the city’s University Bridge (also known as the 25th Street Bridge), which was used for a sushi display at the Congress of the Humanities and Social Sciences at the University of Saskatoon, where the theme was ‘Bridging Communities.’
When taking on his first ice bar for La Bodega, Fogarty began the process by drawing templates for cutting out the logos representing the various corporate sponsors. He first photocopied each logo onto a piece of acetate, then used an overhead projector to beam the logos onto paper at actual size, so he could trace and sketch out the designs. This phase of the project took about four days.
Next, Fogarty glued each sheet of paper onto the corresponding block of ice, so he could cut out the logo by manually following the lines of the design. The accuracy of this approach was limited by the degree to which he could make repeatable cuts by hand.
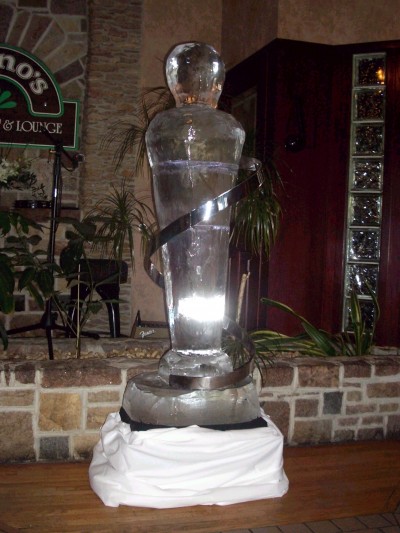
“The potential for error was huge,” he says. “If I made even a slight cutting mistake, I had to start over with a new block of ice!”
Fogarty worked in a freezer, set at just -5 C (23 F), when cutting out the logos. As he progressed, he replaced the cut-out areas with a mixture of gelatin and finger paint to provide the corporate colours. It took four days to cut out the logos, along with the pillars and tops of the bar.
An extra two days were needed for assembling the ice bar. During this phase, Fogarty had to make the final cuts that enabled all of the pieces to fit together.
Moving to computers
In 2008, Fogarty began computerizing his ice-carving operations. The process was fast. By 2010, he was producing nearly all of his work using CAD/CAM software and a CNC ice router.
“I selected the software because of its ease of use, particularly for converting existing artwork from our clients and then sizing, positioning and mirroring their logos,” he says.
Indeed, for the 2010 ice bar, Fogarty received electronic versions of the sponsors’ logos, rather than using drawn templates. He preferred vector artwork, because it eliminated the need for an extra step of converting bitmap art to vector format; but in cases when he did receive a bitmap file, he was able to use the CAD/CAM software to convert it accordingly.