Adding logos to ice sculptures
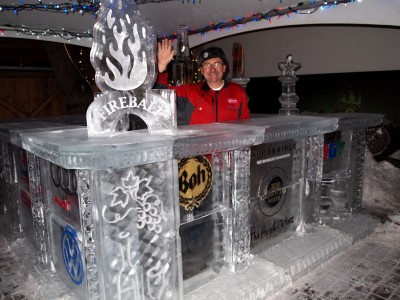
By Jerry Fireman
For several years running, La Bodega Tapas Bar and Grill in Regina has commissioned an annual ‘ice bar’ to be sculpted on its outdoor patio. This winter tradition is part of an effort to raise money for Regina Transition House, a local emergency shelter that helps women and children affected by violence.
By way of example, the ice bar built for the 2010/2011 season was assembled using 40 blocks of ice and weighed some 5,443 kg (12,000 lb). It was functional from the last week of November 2010 until the third week of March 2011.
The ice bars are built by Peter Fogarty of Fire and Ice Creations in Saskatoon. His first in 2007 required 10 days of work, as he manually designed, cut and assembled the structure with logos representing 10 corporate sponsors. It took four days to design the logos by hand, four more days to cut the pieces of the bar and two days to assemble it all together.
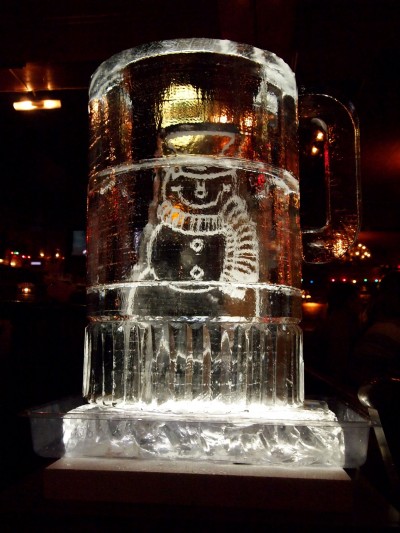
Since then, however, technology has made the work go more quickly. In 2010, using computer-aided design/manufacturing (CAD/CAM) software and a computer numerical control (CNC) ice router, Fogarty designed and cut 20 logos for a much more complex ice-bar structure in just seven days. This period included two days to design and position the logos, four days to cut the blocks of ice and less than a day to assemble the bar on-site.
“The software greatly reduces the amount of time required to size, position and produce a mirror image of each logo,” he explains. “This is required because the logos are cut out of the back of the ice blocks.”
Getting started
Fogarty began Fire and Ice Creations as a side business in his garage in 1999, when he was focusing most of his attention on a distinguished culinary career as a chef, but he already had a longstanding enthusiasm for the ice carving.
“I saw it for the first time at a demonstration in 1977 and I was hooked,” he says.