Dark and reflective surfaces
Beyond clear media, the ability to print white ink onto dark or reflective surfaces is beneficial with the advent of direct-to-substrate graphics. Many new UV-curing printers, for example, are engineered to direct-print not only flat substrates, but also dimensional awards, packages and giftware, among other promotional giveaways and consumer and industrial products. White ink is even used to print logos, serial numbers and text directly onto the housing of tablet computers and other electronic devices.
Production
Working with white ink is straightforward once signmakers understand its performance characteristics.
Profiling the media, for example, is very important. Most designers think of profiles for their colour characteristics, but they also provide the balance between heat settings, ink load and production speed for the printer. Hence, the symptoms of a poor profile tend to show up as issues with drying time, opacity or adhesion.
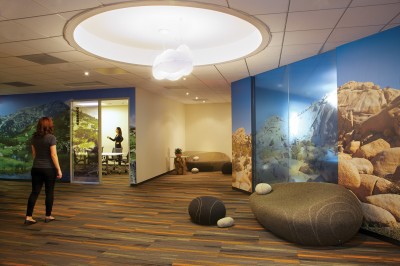
White ink is often printed onto clear media for applications that require some level of translucency, such as glass dividers, doors and windows for interior décor projects.
Sign shops have the option of either profiling preselected media or choosing substrates that have already been profiled for the printer in question. This is why many printer manufacturers offer their own media line, designed for optimal results.
The more opaque a white ink is, the better the results. To achieve a high level of opacity and brightness, however, white ink particles are typically much heavier than those for cyan, magenta, yellow and key/black (CMYK) inks, so white ink has a tendency to settle within the printer. It thus needs to be circulated to maintain high quality.
For this reason, an automated ink circulation system is recommended for the proper management and dispersion of white ink. These systems help minimize the need for—and cost of—printer maintenance over time, while also ensuring the highest print quality across applications.
Finally, the printer’s raster image processor (RIP) software should recognize the unique properties of white ink. Compatibility in this area will make for much easier printer operation.
Clear ink: A premium finish
Clear ink has been one of the most exciting innovations for industrial printing, as it can add brilliance, texture and dimension to an ordinary graphic.
Available only for UV-curing inkjet printing devices, clear ink has been in high demand for the packaging and labelling industries, as well as for some specialty graphics. One reason for this popularity is it allows PSPs to replicate some of the most complex graphic finishes that have traditionally been generated by offset printing, but with the greater simplicity of inkjet technology.
Applications
Clear ink can be used to provide a simple matte or gloss varnish for a logo, photo or background colour; to create eye-catching reliefs and other tactile effects that encourage passersby to reach out and touch the graphic; to achieve simple embossing effects for a premium appearance; to print functional Braille dots; and to add special effects, such as faux water droplets on a champagne bottle label to simulate condensation.
Maxwell Dickson, an interior décor company, relies on clear inks when finishing the surfaces of coffee tables, which also integrate full-colour printing on tempered glass. The clear ink adds texture and durability.
Indeed, enhancing durability with clear inks is particularly important for any graphics that are handled on a regular basis, as coffee tables are, or exposed to outdoor elements.
Production
Working with clear ink is easy today. Most major graphic design software suites allow it to be integrated directly into image files.
Advances in RIP software have also made it easier to reproduce textures and patterns with precision. Some offerings include a specific pattern and texture library for clear ink, allowing signmakers to achieve reliable, repeatable results.