All you need to know about banners
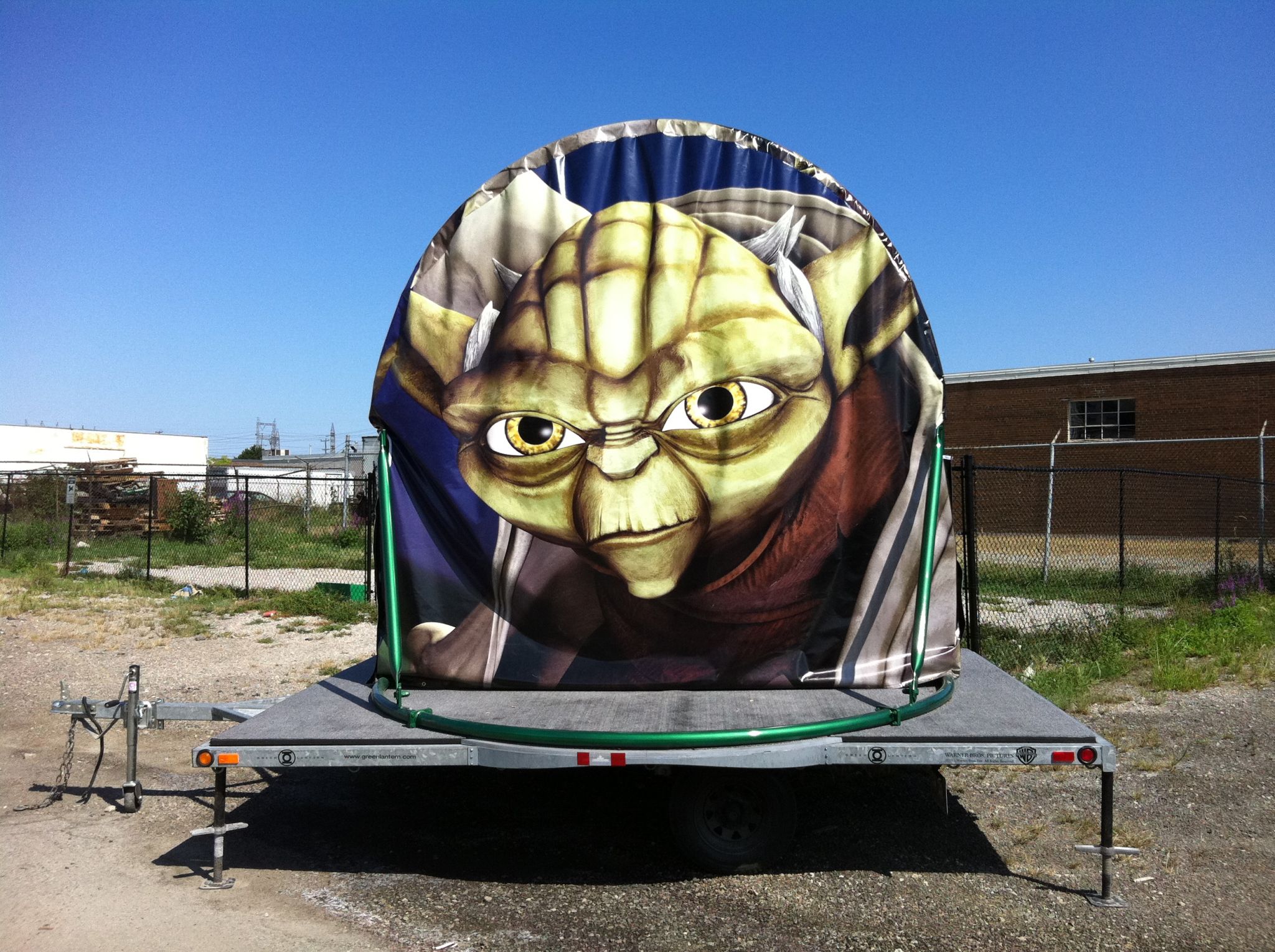
By Arash Ejtemaee
While many sign shops are branching out into new and unusual markets, industry surveys show the number one wide-format printing application by volume is still banners. Nevertheless, signmakers young and old alike often ask the same questions about this medium, including how to select the right flexible substrates and inks, finishing options for durability and esthetic enhancement, tensioning hardware and installation methods. It is important to stay refreshed and current on banner basics.
With that in mind, the following are some technical tips and techniques based on common concerns for large, small and specialty sign shops.
Layouts
The old phrase ‘time is money’ is especially true in the banner business. Both time and money can be saved by following these simple rules for banner layouts:
- Print all of the trim/cut lines right on the banner. It is easy to drop these lines into the design file all at once and much harder to mark them manually on every single banner on the floor. Note that crop marks are not considered cut lines.
- Also print little marks wherever grommets will be installed.
- Print a faint fold line for pockets.
- When printing multiple banners on the same substrate, do not leave space between them. If two banners can be separated with a single cut instead of two, half the labour is needed.
- Allow a minimum of 25 mm (1 in.) overlap for multi-panel banners; and leave an additional minimum 25 mm of white material beyond the overlap for seaming and/or welding.
Back-to-back banners
The double-sided outdoor banner may be one of the oldest forms of signage, dating back hundreds of years to hand-sewn appliqués and hand-woven silk. By now, though, signmakers ought to be able produce them more efficiently. Doing so begins with laying out the print file.
(Note: the following guidelines are intended for outdoor banners only. For indoor banners, it is better to print on both sides of a single piece of blockout material, for a truly double-sided application.)
It is not unusual, while driving through a city, to look up and see the remains of a double-sided pole banner on a lamppost, flapping in the wind, shredded to pieces, with its bottom arm missing. One may well wonder whose windshield it landed on!
Most, if not all, outdoor double-sided banners end up installed on arms or brackets on a pole or wall. It is important when finishing a pole banner to avoid leaving a single point of failure (SPOF).
To make sure they last beyond the first windstorm, it is best to print them as two single-sided banners and then finish them back-to-back as one. This can be accomplished in the following manner:
- Print on one side of two pieces of material. Compared to printing on two sides of one piece, this is a much easier option, both for printing and for finishing.
- Print the graphics from ‘head to head,’ so the material can be folded in half to create the banner.
- Reinforce the sides of the banner with seatbelt webbing when sewing them together.
- Make sure the seatbelt webbing goes through the pocket and loops back down.
Today’s file layout procedures help make this option possible, while also providing a great yield on banner vinyl, no matter which width of roll is used:
- With a typical example of a customer’s requested double-sided banner (see Figure 1), the dimensions are all inclusive; this means the measurements are taken from the outside edge of the finished material, including the pockets.
- The print file should be designed to make it easy to line up the two sides (see Figure 2). Then, when it is time to finish the banner, it is simply a matter of folding it in half from the top. This means fewer seams, which in turn means fewer weak spots.
- The layout phase also involves nesting banners on the roll for the optimal yield (see Figure 3), with no white space between them. As mentioned earlier, this technique reduces cutting time significantly.