Channel letter production reaches new heights
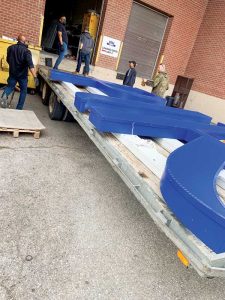
Building on experience
We were met with another challenge when a company asked us to build crane signs which would need to be installed before the crane was raised on a construction site. Again, we needed to ensure strength of fabrication, since the letters would be installed approximately 70.1 to 80.7 m (230 to 265 ft) above the ground. As a result, their ability to withstand the wind load was of the utmost importance. This request came with the need to build a welded mounting frame, for safe transportation to the site.
The layout and design were also highly important to this client. The letters would be very visible to passersby, so brighter illumination was used to draw more attention to the signage. In addition to the specific details which would need to be attended to, crane sign projects have to be completed within the very tight and firm deadlines of their respective construction projects.
In situations like these, it can be tempting to compromise on attention to detail, colour matching precision, and overall cleanness of appearance, due to the large size of letters and the height at which they would be installed. While some people claim no one can see an imperfection from way up high, our team strongly believes if we are not happy with it, our customer will not be happy with it, either.
We work diligently to ensure we pay close attention to every detail. In our painting process, we use colours from our colour matching paint system, seek help directly from paint suppliers if we are not confident we can get an exact match on our own, and leave our paint jobs to cure for an extra few days—just to make sure there are no fingerprints.
The next five years
Over the last five years, Atara Signs has taken the approach of listening to our clients’ needs, to ensure we understand their expectations and the details of their order. There is no job too large for our team—in fact, we are already reviewing a 4.2-m (14-ft) tall channel letter project with a client. To ensure the best possible result, our customer service and design staff may suggest alternative materials, products, or services which are more cost-effective or give better quality to our clients. Once the final order and cost have been approved, skilled production staff create the custom orders, combining up-to-date technology and traditional craftsmanship to meet specific needs. With this approach, we have ended up with happy clients and repeat orders. We will continue to strive for excellence in customer service and quality of product in the next five years.
Dionne Greaves is the manager at Atara Sign Manufacturing Corp. (Atara Signs). Over the last four years of starting with the company and entering the sign industry, she has gained a true enthusiasm for manufacturing in signage. With a background in customer service and project co-ordination, Greaves’ creative mind helps to shape all the projects that go through the facility. She is looking forward to the years to come in the sign industry, with developing technology and advancements.