CNC Routers: Optimizing cutting and avoiding pitfalls
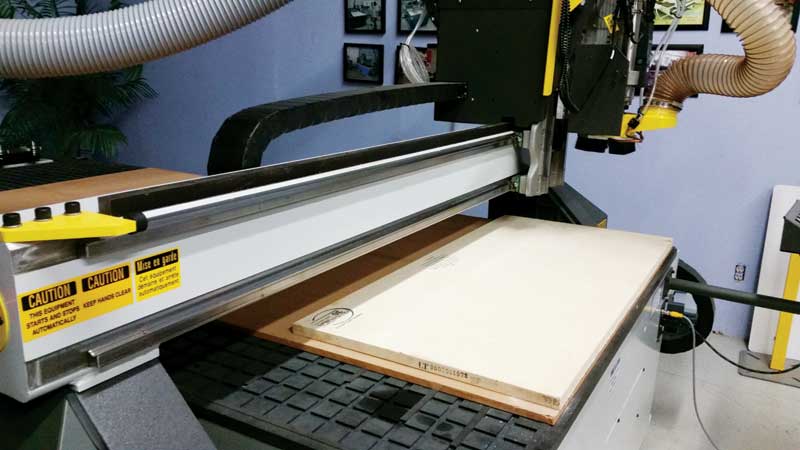
By Peter Saunders
A computer numerical control (CNC) router is one of the most expensive investments a sign shop can make. A thorough process of due diligence is essential before purchasing, as a number of issues could otherwise result in unnecessary costs and a loss of time and materials.
Planning the purchase
Buying a machine with either more or less capacity than needed, for example, will not be cost-effective. Axyz International, a router manufacturer based in Burlington, Ont., recommends buyers seek expert advice in this regard, so they can choose the right processing area for their shop.
That said, it is also important to plan for future production requirements. A router can play a major role in a sign shop’s growth, so its capacity should match reachable goals.
Multiple materials require different cutting heads and tooling. This plays into choosing a router that can (a) process different substrates and (b) use a variety of cutting options. Selecting the right accessories and options is a priority at the outset for keeping costs down in the future. And spare parts need to be easily available.
Further, a router should be capable of evolving alongside technological developments, i.e. by being retrofitted and upgraded—not only with tooling options, but also in terms of its operating system (OS) and software.
Feed rate
Due to the diversity of materials processed by today’s CNC routers, it can be easy to run into machining problems when producing signs and graphics. One of the crucial steps in optimizing a router for cutting, ensuring a better finish and saving money through less breakage of cutting bits is to determine the right feed rate.
Paul van der Velden, a support technician for Multicam Canada based in Concord, Ont., explains the formula for calculating the feed rate for a CNC router is to multiply the machine’s speed in revolutions per minute (RPM) by its chip load and number of flutes. This process may sound simple, but it is not necessarily straightforward at first, so it is worth going over the variables step-by-step with relation to different materials.
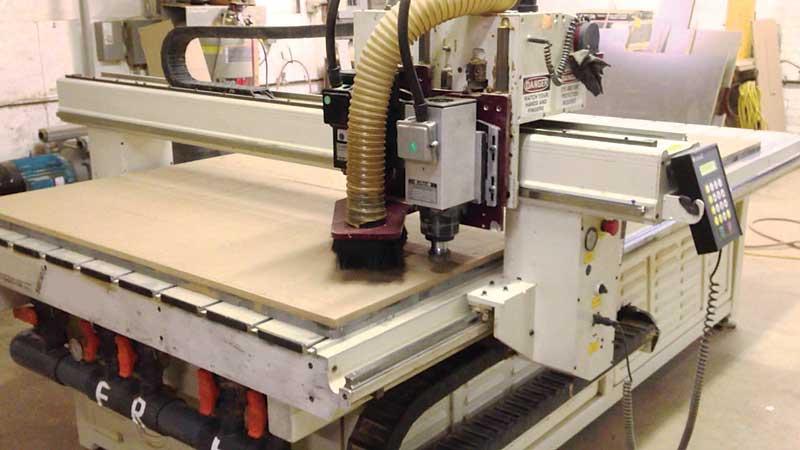
Photo courtesy Axyz International
RPM
Most CNC router spindles are capable of between 20,000 and 24,000 RPM. A lower speed is recommended, however, to help optimize the lifespan of the spindle.
A good industry average to aim for is approximately 18,000 RPM, although this may vary depending on the material being cut. With nylon, acrylics and many other plastics, for example, it is a good idea to keep to the lower end, perhaps 17,000 to 18,000 RPM. Too high a level with a low feed rate could lead to the plastic melting.
(It is important to note not all plastics are created equal. When using the proper bit and speed, flexible plastic will curl a chip, while rigid plastic will produce a splintered edge, but even a simple change of colour can drastically alter the way the material reacts to a cutting tool. With that diversity in mind, the shape of the cutting tool is crucial.)
At the other end of the spectrum, when a sign shop is cutting stronger substrate materials like aluminum, a speed of approximately 20,000 RPM would be more suitable. And it is worth keeping in mind that while the chip load and number of flutes cannot be adjusted once a tool bit has been chosen, the speed in RPM can always be changed.