CNC Routing: Choosing the right cutting tools
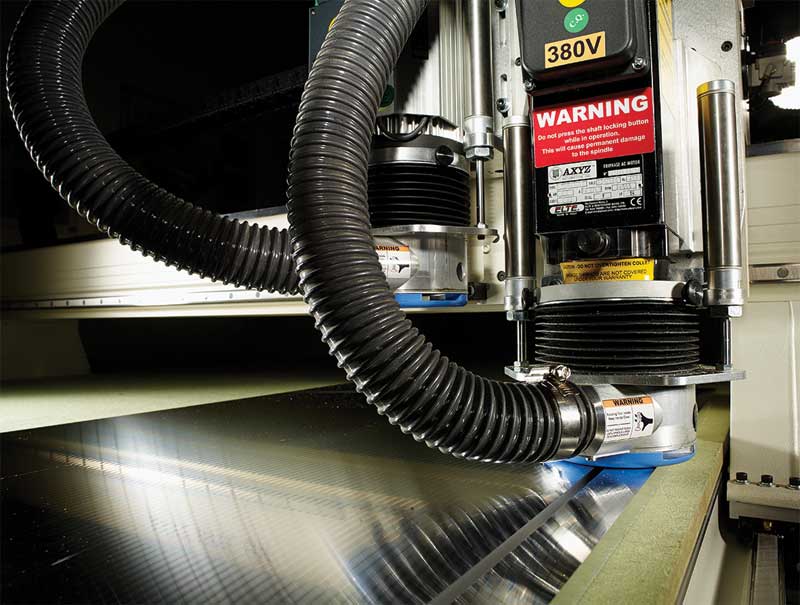
Substrate-specific selections
Cutting aluminum, by way of example, typically calls for an up-cut spiral router bit geometry, which is designed to push the chips and debris from the cut upwards, where they are collected by an extraction system, like a vacuum. This setup helps ensure a cleaner cut, as well.
There are variations among different up-cut tooling options, including the angle of the spiral itself. Some tool manufacturers offer dedicated bits that are designed specifically for aluminum. These should always be the starting point in the selection process, as they generally result in optimum results.
Often, but not always, manufacturers also recommend the use of lubricants when cutting aluminum, in part to extend the life of their router bits. Before lubricants are used, it is important to make sure an automatic misting system is fitted to the machine. This will ensure a consistent and accurate application of lubrication, which is essential for consistent cutting results and extended tool life.
That said, there are tools available that are designed to cut aluminum without using a lubricant. These can offer such benefits as reduced post-routing cleanup time, which
may be an important consideration in a busy sign shop.
For aluminum composite materials (ACMs), which can be grooved and folded, at least two cutters are typically required: one for routing and one for grooving. The latter operation often requires a sharply angled V-cut too, but another option is a ball-nose bit, which is circular on the bottom.
Down-cut spiral router bits, meanwhile, can be used on very thin, flexible aluminum stock, where an up-cut design would tend to lift the material itself off the routing table, causing it to vibrate or move slightly, possibly ruining the cut and throwing it out of tolerance. A down-cut spiral router bit helps push the material down toward the table’s surface, where a vacuum or clamping system can also help keep it in place during cutting operations. The up-cut spiral router bit is typically the tool of choice for aluminum sheets that are thicker than 0.76 mm (0.03 in.).
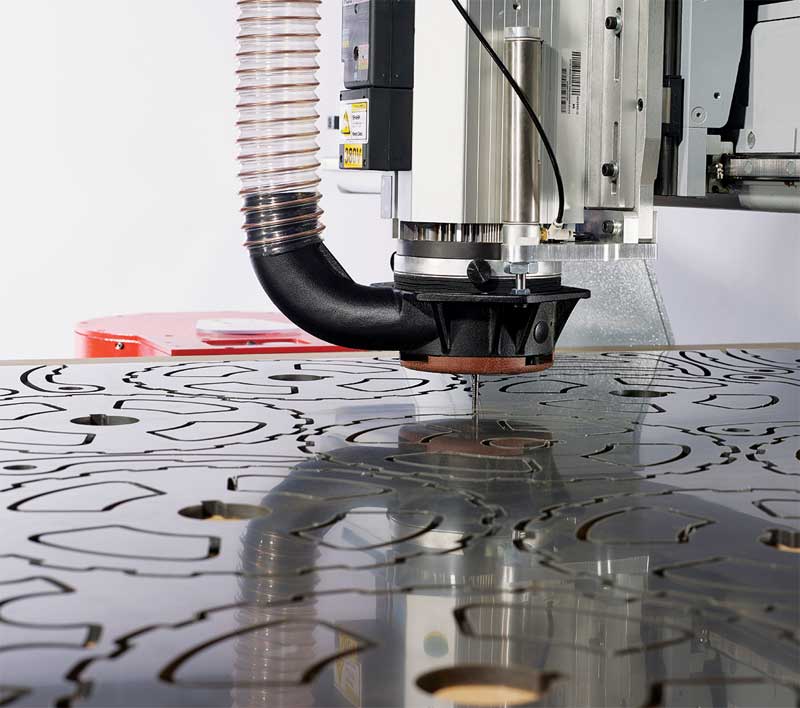
Resin-based medium-density fiberboard (MDF) can be easily cut using an upward spiral router bit, but cutting wood will always involve some variables, of course, depending on the composition of the product. Wood-based sign substrates range from simple plywood to chipboard.
Another factor to consider is whether or not the material to be cut has been laminated or processed with a veneer on the surface. In such cases, it is better to use a straight-fluted or compression bit, which will not lift the cut material up off the surface; whereas an up-cut spiral flute could chip the top surface when cutting a wood-based stock. CNC router manufacturers will often recommend the compression bit, a tool that combines both up-cut and down-cut geometry and tends to push the cut material toward the middle, reducing the chance of chipping the top and bottom edges of wood.
When it comes to routing plastics, such as acrylic, the recommendation is an up-cut router. Indeed, the choices are much the same as with aluminum, but with slight differences in the tooling geometry.
Single up-cut spiral-fluted cutters are the ideal choice for plastics. As with aluminum, however, the down-cut spiral design works better for very thin plastic stock, since the up-cut router would tend to lift lighter material off of the table.
Down-cut spirals are also a better choice when cutting out very small parts, since they will push those routed parts down toward the table bed, instead of trying to lift them like debris due to their minimal surface area.