It can be very effective to use a silver flake and tint the base ink. By using the same flake in a variety of colours, cleaning out all of the flakes from the screen and squeegee becomes a non-issue.
Also, colours can be combined to achieve corporate or specialty matches. Ideally, the ink will be highly transparent, to allow the glitter to sparkle through, and highly saturated, to enhance the visual impact.
Several suppliers even provide premixed glitter inks. This prevents the need for mixing in the shop, but still allows an opportunity to add other powders for further special effects, such as fluorescence, pearlescence or interference.
‘Transparent’ glitter powders tend to appear white and can achieve an extremely high level of sparkle at a low load level of just 0.5 to one per cent, which also means a smoother ink surface. They are chemical- and heat-resistant, with strong outdoor durability. The downside, however, is they are more difficult to source than metallic powders, typically requiring large orders at high prices.
Inks and clears
A range of inks and clears can be used to provide or highlight special effects. For ease of use, most print shops today source UV-curable versions of these products, though solvent-based formulations are also available in many cases.
Transparent inks
Mixed, halftone and spot colours usually have some degree of opacity or haziness. In most applications, this opacity is not apparent, but transparency can become important when printing certain effects onto clear substrates.
With increased transparency, a higher level of metallic sheen, for example, can be seen through overprinted colours. This is especially important when multiple layers of ink—as in a four-colour process image—are printed with a metallic effect. Using various halftone combinations, gradations can be achieved across a graphic.
The trick is to determine the limitations of combining inks within the same image. Fortunately, software has made this much easier than before.
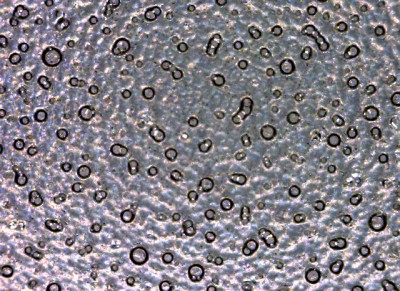
Clear inks that retain tiny bubbles in the print can result in a fine textured effect not easily reproduced by other means.
Highly transparent colours also require a greater level of saturation to ensure the image ‘pops.’ Higher-density screenprinting inks will retain their colour when backlit on clear substrates.
Transparent inks can also be used as single-pass colours over metallic effects, either in colour matches or ‘as is’ out of the container.
Textured clears
Textured clears contain large particles to produce a rougher surface. They have been borrowed from industrial applications to add tactile features to printed graphics.
Textures range from a satin/suede to abrasive/gritty. With most textured clears, a rougher surface requires a coarser mesh, to allow the large particles to transfer through.
The larger particles are so good at resisting physical abrasion, the screenprinting of the ink can in turn prove somewhat abrasive to the squeegee and screen. A thicker, more durable stencil, paired with a tougher squeegee, should be able to stand up to textured inks.
Bubble clears
Most inks are formulated to flow out smoothly. Clears that retain tiny bubbles in the print, however, can result in a fine texture and a visual effect that is not easily reproduced by other means.
The trick with using this type of clear is to define the mesh and a consistent printing process. There is a certain degree of processing latitude and the resulting bubbles will be somewhat random, but printing through a finer mesh will result in finer bubbles, while a coarser mesh will produce coarser bubbles.