Digital Printing: Dispelling five myths around the simplicity
Myth No. 4: The print material is always the problem
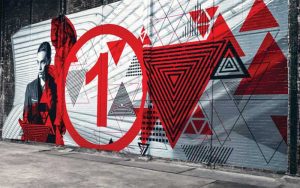
Troubleshooting effectively is a significant part of the printing process. When one faces a problem during printing, one must be able to determine if the material, printer, or a foreign factor is the reason. Simple diagnostics can help speed things along when issues arise.
For example, if there is banding on the print, the first step should be to conduct a head check and cleaning. If the issue persists, one must check the media by rotating the material 90 degrees. If the banding is horizontal, it would point to a printer issue. If the banding remains in the same direction as it was earlier, this points toward the material as the problem. The next step would be to load a different material and test for banding. If one suspects the material is the problem, one must reach out to their print media provider for assistance who can help work through any additional troubleshooting steps while also checking against retained material on their end.
Myth No. 5: The tough part is over when one gets to finishing
Proper finishing depends on who is working with the material. Today, with trimming and weeding equipment gaining popularity, many shops have implemented automation into finishing. Yet, many shops continue to depend on a dedicated staff to handle this function manually. Precise straight-line cuts allow clean installations and create perfectly straight overlaps. Production personnel and installers must work together to align panels, as often, no bleed is given to the installer who, as a result, seams the material improperly.
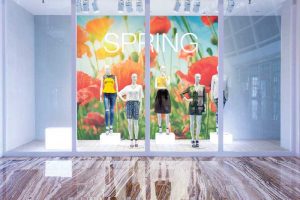
Knowledge of merging different media when laminating the material is crucial. For example, what should be done if a laminate shows diagonal lines running across the film? In this case, one should be able to diagnose the way the lines run across the material from the laminator; this will help provide information on how to resolve the problem. Perhaps, the nip roller is out of adjustment. The laminator rolls must have equal pressure on both sides; otherwise, there will be tracking issues and inadequate pressure on one side of the laminator.
When laminating, one must test each side of the roller by sliding a piece of paper in and out between the rollers, tightening it until it stops moving. This must be done on both ends until the friction is equal. After it has been adjusted, the material can be reloaded and tested. It may be necessary to contact the laminator manufacturer for service as some adjustments on laminators should be completed by authorized personnel only.
Digital printing requires skill
The process of transitioning a project from
an art file to a physical print is complex and requires hard work, talent, and knowledge. Producing a quality item that will survive its intended lifespan not only requires the right equipment and media, but also specialized understanding and experience working through its unique challenges. The job is not always an easy one.
Ryan Allen is regional technical specialist for Avery Dennison Graphics Solutions in North America. He holds a degree in graphic design and has more than 12 years of experience in design and print production. He previously owned print and wrap shops. Allen can be reached at ryan.allen@averydennison.com.