Keeping up with demand
In some cases, an existing digital inkjet printer is modified by removing the pinch-roller system and replacing it with a solid-roller fabric-handling system. This allows a wider variety of fabrics to be used in a single printer and also reduces the likelihood of head strikes (i.e. when a printhead comes into contact with the media) that can occur with textile-based substrates.
Some printers use a staggered head platform to help increase the amount of fabric that can be printed per hour compared to earlier machines. As the demand for output rises, sign shops can move up to faster printers like this and/or run multiple entry-level printers together.
Spoonflower, for example, is a large-format printing company that lets its customers design their own printed fabrics online for applications like banners, curtains, clothing, bags, framed artwork, pillows and furniture. Since starting up in 2008, Spoonflower has added multiple digital printers—modified by adding a fabric handling system to the base digital inkjet platform—using water-based pigment inks.
In four years, the company has grown from one beta-testing unit to 20 printers. This setup allows multiple projects to be printed at the same time.
Some sign shops both move up to a higher-speed fabric printer and keep their entry-level model for sampling and short print runs.
Fixing to fabric
Once an image has been printed, it needs to be fixed to the fabric. With heat transfer processes, a mirror image is digitally printed onto high-quality coated transfer paper, then run through a heat press to transfer the image onto a polyester fabric, which does not need to have been pretreated to accept the image.
The same equipment used for heat transfers can also be used to fix direct-printed fabrics. In fact, dry-heat fixation is used for direct printing, for pigment inks that contain a binder for printing onto uncoated natural fibres and for pigment inks without the binder.
Another method of fixation, which has become common in Europe, is to steam, wash and dry. This process is effective for applications where ink penetration is important using reactive and acid dyes.
Which method of fixation is best will depend on specific market needs. Each option can be equally cost-effective.
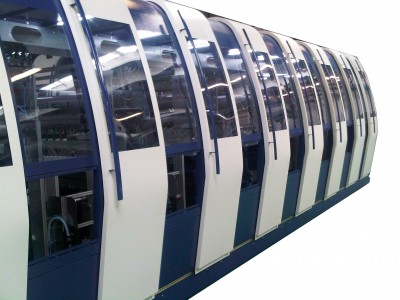
Single-pass continuous digital printing—whereby the substrate moves and the printheads remain stationary—is replacing traditional rotary printing in the fabric industry, as it is proving simpler, more versatile and more reliable. It is also more flexible, as colours and designs can be changed on the fly.
Determining ROI
Before buying a printer, it is important to determine the rate of its return on investment (ROI). Assuming a relatively busy workload and knowing the machine’s average printing speed, profits can be estimated per machine-hour by calculating sales revenue based on price per square yard, then subtracting costs for the fabric, heat transfer paper, ink and/or other consumables, along with labour costs for the printer operator.
If, for example, a machine is printing 8.4 m (10 sq yd) per hour, its output sells for $20 per square yard and the fabric, ink and overhead costs total $10 per square yard, then it should yield a profit of $100 per machine-hour. This rule of thumb will help printing assets be managed so as to maximize their money-making potential.
Ann Sawchak is a managing partner at Expand Systems, which modifies Mutoh America inkjet presses for direct digital printing onto fabrics. For more information, visit www.expandsystems.com and www.mutoh.com.