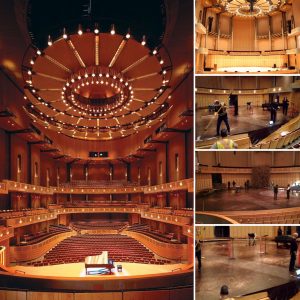
Vancouver-based full-service commercial printer Still Creek Press recently selected Drytac to produce graphics for the University of British Columbia’s (UBC’s) virtual opera.
Vancouver-based full-service commercial printer Still Creek Press recently selected Drytac to produce graphics for the University of British Columbia’s (UBC’s) virtual opera.
The UBC Opera puts on shows for the local community each year but, due to COVID-19, these programs had to be put on hold, with indoor entertainment venues in Vancouver forced to temporarily close.
However, not to be deterred by the restrictions on audience attendance, the UBC Opera decided to stage several virtual events on Nov. 30, 2020. Students performed at the university’s venue, and the show was streamed live to a virtual audience.
The print shop’s role was to produce floor graphics resembling a dirt road for the stage. The production was filmed from several levels and views, which meant the graphics had to be visible and look realistic from all angles.
“Essentially, we started with an empty stage,” said Still Creek Press’ wide-format manager, Bruce Lee. “We were tasked with installing floor graphics that looked stunning and could be easily removed at the end of the performance. As stages are brightly lit, we also needed a material with a matte finish.”
The company opted for Drytac SpotOn Floor 200 vinyl film for the project, and produced graphics covering an area of approximately 21 x 27 m (70 x 90 ft). Nine rolls of the film were required to complete the project, and the graphics were printed in four days on a Roland Soljet Pro 4 XR-640 large-format device.
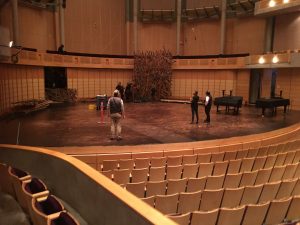
The production was filmed from several levels and views, which meant the graphics had to be visible and look realistic from all angles.
Lee also spoke about the ease of use when working with the graphics, saying it allowed his shop to complete its part of the project in good time, without any delays.“We weren’t the only crew there working on the stage, and this meant keeping our distance from other crews and equipment,” said Lee. “Once a section was complete, we had to switch sides with the other team or wait until they were done with their part.
“What would normally have taken two days to install only took us five hours. We were able to get our part of the production done well before deadline, which meant those working around us had more time to finish their jobs.”