Evolution of the Modern Sign Truck
By Bryan Wilkerson
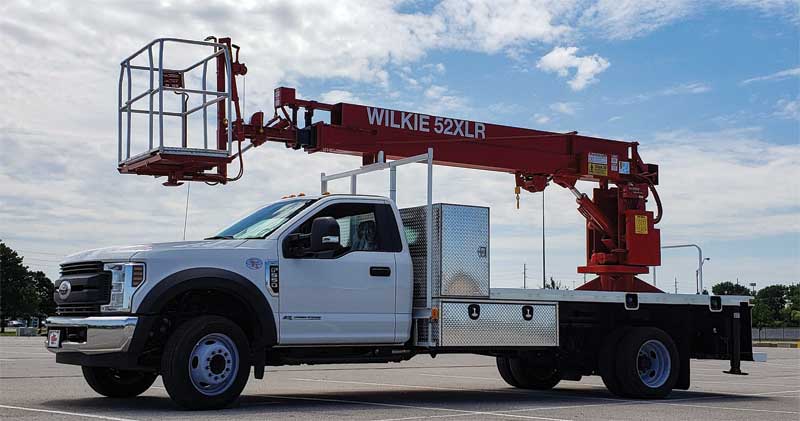
The evolution of the modern sign truck began at the dawn of the electric sign age when craftsmen demonstrated their talent with a mere paint brush. The journeymen of the time performed ‘elevated’ installations using scaffolds, block and tackle, or straight ladders lashed together to reach soaring heights. With time, of course, the size and complexity of signs multiplied tenfold, going from simple circus tent type canvases to large boards, swinging structures and, finally, to modern-day signage, which includes light-emitting diodes (LEDs), motion, changeable copy, moulded accents, and gilding. As times changed, signs, too, assumed enormous proportions; some completely covered the building’s façade, lending themselves to the overall architectural design. These developments led the way to even greater needs, resources, and workload on the part of the sign installer.
Humble beginnings
The gin pole lifting device existed even before the invention of the working sign truck. Here, two parallel poles formed a triangle with a pulley at the end, which was used for lifting both the pole and sign. Most of these sign installation devices were originally driven by hand-crank systems, eventually leading to an electric system—usually of the 12-volt nature. Later models used a power takeoff (PTO) method, which took power from a source (or engine of the truck) and transmitted it to the device. Today, gin pole trucks are no longer seen in the sign industry, primarily due to the amount of time they took to rig a unit. Also, lifting could only be done directly off the back of the truck as it did not allow any rotation or side reach to the equipment. Although these units were very strong and could lift heavy weights, these disadvantages gradually led to them being phased out as more modern and flexible cranes entered the workplace.
The sign installer’s lifting capabilities initially started out with a block and tackle attached to a scaffolding system, slowly progressing to hand-crank driven gin poles (followed by truck-mounted devices), and finally the hand-crank telescoping crane. The latter, too, moved on to electric cranes with 12, 110, or (in some rare cases) 220-volt alternating current (AC). These units eventually gave way to hydraulic cranes, which did not include any rotating or vibrating structures (such as cables rolling over the next reeve in a cable reel).
The smooth actuation of hydraulic cylinders soon replaced previous mechanisms. This new method allowed equal force all the way through the unit’s motion and could also be equipped with a ‘soft’ start or stop. This meant the motion would start off slowly at first, increase in speed, and then slow down at the end of the operation.
Reaching greater heights
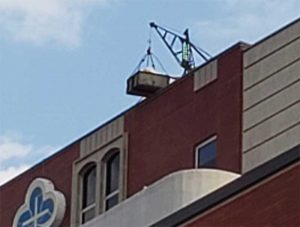
At first, elevation for sign installation jobs was either accomplished with the help of an actuating screw or a hydraulic cylinder. As stem/brass bushing bases gradually moved to ball bearing turntables, truck-mounted aerial ladders started becoming popular for reaching greater heights. These units slowly replaced Boatswain chairs, or swinging planks, that were used at the end of the crane’s load line cable. This chair consisted of a piece of wood secured on either side of the seat and attached to the crane, which would elevate the installer to the desired height. This, however, was dangerous as there was nothing holding the person in place except for (maybe) an extra rope tied around his/her waist and, later on, a safety belt. However, this was not very safe, especially if the installer was distracted or a strong gust of wind began to sway the platform. The worker could potentially crash into the sign he/she was working on, get caught up in the equipment and be suspended by one of their limbs until he/she was lowered to the ground, or (in worst-case scenarios) slip and fall off the platform.
The invention of the modern aerial ladder transformed these situations to a safe and stable one-person job. Here, the raised work platform was fixed to a rigid structure, which allowed greater stability as the installer performed his/her job. This further reduced labour and improved speeds for setup, creating a whole new industry of people that strictly specialized in service installation.