Assembling channel letters
The fabrication of channel letters, whether they use LEDs or another source of interior or rear illumination, remains a major part of the sign industry. Conventional techniques involving cutting a raw material—usually aluminum—into the desired letter shapes and then assembling the final products using screws, rivets or welding. These fastening techniques present some key disadvantages.
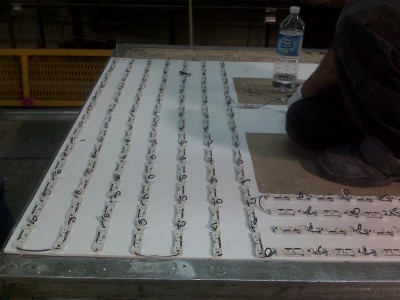
Light-emitting diodes (LEDs) used in signmaking are protected by potting and encapsulation adhesives. File photos
Welding is a costly, time-consuming process that requires specialized training. It achieves full load-bearing strength almost instantly, yet it frequently results in burned or distorted substrates that need extensive post-production reworking. Screws, rivets and bolts, meanwhile, often call for additional joint designs, raw materials for tongues or flanges, pre-drilling and/or filling in screw heads—not to mention the cost of the fasteners themselves.
It is possible today to assemble channel letters using only adhesives. In the past, one of the hurdles was how long it took to achieve load-bearing strength. Acrylic adhesives can cure rather quickly, usually with a handling time—i.e. the period until bonded piece can be moved or handled without breaking the bond—of around 10 minutes. To compensate, special acrylic-based hot-melt adhesives are applied to serve as a ‘clamp down’ device, holding the pieces in place as the structural adhesive cures.
This system has many advantages. It requires no specialized training and very little surface preparation, is esthetically pleasing and involves no damage to the materials. Any stresses will be distributed evenly across the bond line, rather than concentrated in small areas, resulting in greater overall strength.
In addition to substantial savings over welding in terms of time and labour, this process also uses less expensive associated equipment and allows for the use of thinner sheets of aluminum, reducing material costs.
Installing channel letters
Adhesives can also be used for the installation of channel letters and other types of signs into a wall.
First, surface-mount fasteners are bonded to the backs of the letters or sign. These replace the need for drilling or stud welding.
Next, threaded rods of the desired length are attached to the studs. A thread-locking material can be used for additional strength.
Holes are drilled into the wall and filled with an epoxy or anchoring adhesive. While 100 per cent silicone adhesives have sometimes been recommended for this type of application, it is better to select a true structural adhesive.