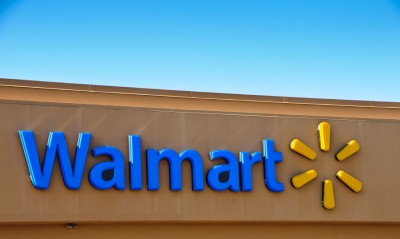
Many of today’s channel letters are assembled and installed with adhesives. Photos courtesy Chemical Concepts
Finally, the sign is placed on the wall, pushing the threaded rods into the adhesive in the drill holes. The backs of the channel letters can either be installed flush to the wall surface or set out using standoffs for consistent spacing from the wall. It will be necessary to temporarily secure the sign with tape or other means while the adhesive fully cures.
For indoor sign installations with lighter loads, double-sided acrylic foam tapes can be used. Installation is easy and the foam tape provides an excellent bond with a clean appearance. It is particularly well-suited for joining dissimilar materials, as the malleable foam allows for differences in thermal expansion in the joint.
Acrylic formulations
Not all acrylic-based adhesives are created equal. Different formulations are available that set at a variety of different speeds and some offer particularly strong resistance to high temperatures. If a powdercoated finish is desired, for example, the sign fabricator must be careful to select an adhesive that can withstand the temperatures associated with this process.
The ‘working time’ or ‘open time’ of an adhesive is the period during which it can be applied and parts can be mated before it begins to set. This is not to be confused with handling time.
Acrylic adhesives are available with working times as short as two minutes and as long as 45 minutes. The latter are most useful when working with larger pieces, where more time is required to apply enough adhesive before two components can be joined. Unlike an epoxy, the speed at which an acrylic adhesive cures does not have a significant effect on the eventual strength of the bond.
One of the common mistakes when using structural adhesives is to push the two components together with too much force. This can squeeze out the adhesive from between their surfaces, resulting in an inadequately thick bond line.
To prevent this problem, some adhesive manufacturers have mixed tiny ‘micro beads’ of glass into their products. The thickness of these beads ensures an adequate bond line, reducing the impact of operator error during the bonding process. The beads also function as ball bearings, aiding in the repositioning of the parts during the adhesive’s open time.
Product selection
There are innumerable uses for adhesives in the fabrication of signs. As in other production disciplines, the most important tool is knowledge, as selecting the right adhesive for the job will usually mean the difference between structural failure and success. Considerations for a sign shop will include substrate chemistry, temperature, joint design, working time, cure time, colour, surface preparation, thermal expansion, safety and local ordinances.
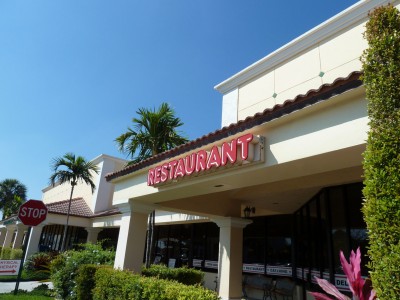
With adhesives, any stresses are distributed evenly along bond lines, enhancing the load-bearing strength of channel letter installations.
As such, it is important to learn about different adhesives and their characteristics. They can roughly be divided into structural and non-structural types. Simply put, a structural adhesive has sufficient strength to bear a considerable load.
Structural adhesives can be further divided into three main groups: acrylics, epoxies and urethanes. Non-structural adhesives include anaerobics, contact adhesives, cyanoacrylates, hot melts, emulsion adhesives, rubber cements, solvent adhesives and sealants, in addition to other, less common types. It is also beneficial to have a working knowledge of industry-standard sign materials and their respective properties. Adhesive manufacturers and distributors should offer free consultation for both the selection and the application of their products.
Surface preparation is often minimal, but a clean, dry and rough surface is generally recommended to ensure a strong bond. Joint design should also be considered, as these principles often differ for an adhesive joint compared to a mechanical joint. Adhesive joints are designed to maximize surface contact area and to minimize exposure to stresses like peeling and cleaving.
From LED potting to structural adhesives, new technologies and applications are constantly being developed. As the demands of the sign industry change, so too will the means of construction and installation. An increased familiarity with these chemicals and their uses can only serve to improve the end products and boost profits for sign shops. Ongoing education about modern adhesive products and practices is a worthwhile investment.
Andrew Morris handles inside sales for Chemical Concepts, which distributes adhesives, silicones, specialty chemicals and fasteners. For more information, visit www.chemical-concepts.com.