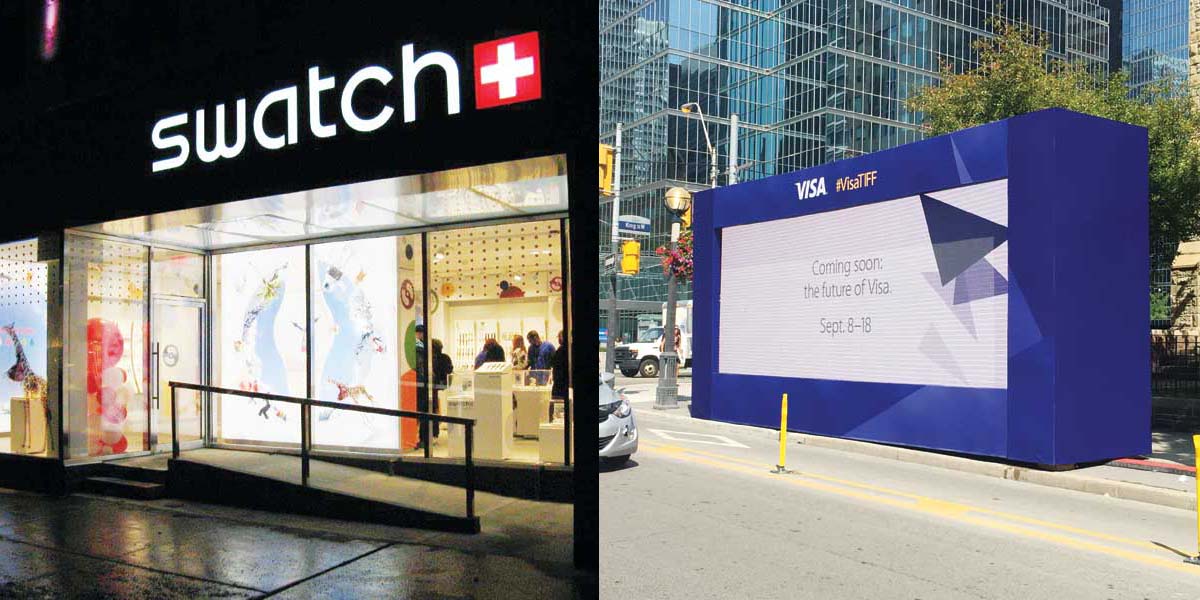
Today’s projects may involve a variety of fabrics printed at a large scale, raising the question of how they are to be cut and finished accurately and economically.
Photos courtesy PNH Solutions
Driven wheel
A ‘driven wheel’ rotary system is a cost-effective method for finishing a variety of textiles. A motor-driven decagonal (i.e. 10-sided) blade chops through each fibre or thread, so as to reduce friction and drag while cutting.
“We researched what to buy for fabric finishing for a long time,” says Francois Hudon, managing director for PNH Solutions, an outdoor marketing, exhibit and fabric printing company headquartered in Montreal. “We visited multiple vendor sites and looked at workflow and support before finally deciding to buy a driven wheel cutter. It has been good for us and, with our increased volume, we will add a second as soon as we move to our new facility in early 2017.”
While some firms are completely digitally oriented for fabrics, the ability to handle other substrates may also be important. In PNH’s case, after buying a driven wheel system for fabrics, the company added a drag knife for vinyl.
Laser
Laser cutting has also been introduced in recent years to help seal the edges of fabrics. A liquid-cooled carbon dioxide (CO2) laser with intensity control can avoid leaving dark edges in most fabrics.
“We have other cutting tables, including one with a driven wheel, but the capabilities of laser really made the decision to buy it easy for us,” says Jason Ahart, chief operating officer (COO) for Olympus Group, a custom large-format digital printing and mascot uniform manufacturing company. “The laser can handle all of our large- and grand-format dye sublimation fabric cutting needs. And today, almost all of our other fabric cutting is done on the laser system, too.”
In addition to avoiding the frayed edges that can come with traditional knife cutting and routing capabilities, the fine nature of a laser is advantageous for precision-cutting graphics with small inside and outside arcs. With contactless systems, the laser does not cause any bulges in the material and can guarantee filigree (i.e. delicate) cuts right from the beginning.
“Our 3.2-m (10.5-ft) wide laser cutter was definitely the correct decision,” says Mike Lecus, president of Imagine Express, which specializes in large- and grand-format ultraviolet-curing (UV-curing) printing and dye sublimation, as well as small-format digital and offset printing. “It’s a solid machine that paid for itself in just a few months. We can laser-cut and get finished edges on most of our polyester-based fabrics as fast as we could with the driven wheel. And because of increasingly varied shapes being cut in fabric, including notches, we now only do rectangular cutting with the driven wheel and all the rest on the laser.”
While lasers can finish a broad variety of flag fabrics, meshes, satins and knitted textiles, they do have limits. They may not be able to cut fabrics coated in polyvinyl chloride (PVC), heavy-duty fabrics for doubled-sided printing, heavy weaves and fabrics containing cotton.