Wood
There are hundreds of tooling options for cutting wood. The choice will depend on the species of tree and whether it is classified as hard or soft. It will also depend on the level of finish required.
When working with wood that is quite porous, such as oak, routing can result in tearout, i.e. splintering of the edges. In such cases, several slower, shallower cuts are recommended.
MDF
MDF is a very popular structural material in a wide variety of sign projects, but it is also very abrasive to cut, so it can pose a threat to tool longevity. This is because highly abrasive materials can generate a lot of heat during cutting, which can lead to tool degradation and spindle damage, not to mention poor cut quality.
To help reduce heat around the routing tool, it is important to choose a bit that will create more chips, not dust. Carbide-coated compression tools are recommended above weaker higher-speed steel (HSS) tools. And if a sign shop is cutting MDF very frequently, it will be worthwhile to use polycrystalline diamond (PCD) bits which, over time, will yield a strong return on investment (ROI).
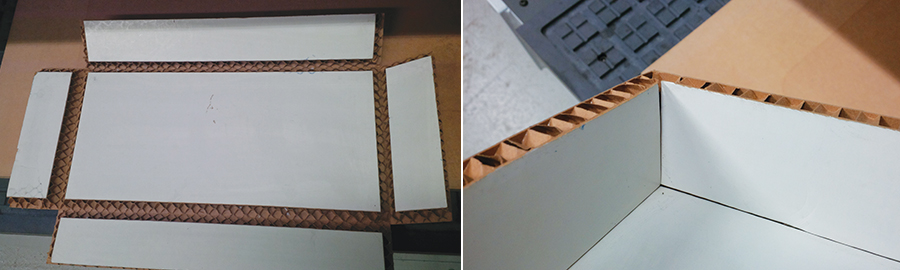
A V-groove knife is used to cut grooves at a 45-degree angle, which allows operators to then fold the two edges together to form a clean 90-degree angle to create frames or displays for signs.
Acrylic
When cutting small or thin pieces of acrylic, it may be a good idea to enhance the CNC router’s hold-down system. A vacuum system is important, but adding some double-sided tape might also help.
It is certainly advantageous to use acrylic-specific bits. Chip removal is much more important when cutting acrylic than when cutting wood or similar materials. This is because plastic chips can melt under the heat of routing and then re-attach themselves to the main piece, so the operator needs to make sure they are cleanly removed from the cutting area.
How acrylic is cut also depends on the desired edge quality. If a crystal-clear edge is needed, than routing can prove difficult. PCD polishing tools are available that can create a nearly optically clear edge for acrylic, avoiding the need for flame polishing, but for shops that are constantly cutting acrylic and need a clear edge, laser cutting may be the best way to go.
Aluminum composite
Aluminum composite panels are very popular among signmakers because they are light, durable and easy to work with. While they combine layers of different materials, the aluminum itself is sufficiently tough that solid carbide tools are essential for cutting it. Coated tools will hold up better, too, ensuring greater longevity. That said, some tools designed for cutting plastics will work well on aluminum composites.
Tools that are 6.4 mm (0.25 in.) or smaller in diameter and have fewer than four flutes are recommended. Aluminum creates large chips when it is routed and a tool with too many flutes can cause jams and even break the cutter.
Another issue is how heated aluminum tends to weld itself onto the tool. Once a tool is gummed up like this, it is useless. So, it is all the more important to clear chips with a vacuum, mister and/or blaster. Making a large number shallow passes, rather than fewer deep passes, will also help with chip extraction. Finally, a slow feed rate can start to cause rubbing, which then heats up the tool and can dramatically reduce its longevity, so it is important for the operator not to ‘baby’ the cut.
Foamboard
High-density urethane (HDU) is often known in the sign industry as foamboard. And indeed, it routs similarly to a foam type of material, so heavier cuts are better.
This means the tool needs more material to grab, so it is important to ensure cuts are at least half-diameter passes. Again, constant chip flow is important.
For highly detailed three-dimensional (3-D) routing, an endmill should be used for the rough passes and then a ballnose bit for the finishing passes. HDU is a great material for 3-D routing and relief production and it can easily be coated and painted afterwards.
How do I cut that?
These are just some general tips for commonly used sign materials. Identifying the type of material to be cut, the best-suited machine to cut it and the specific tool for the job are all important steps in ensuring the best quality for the application. By working with CNC machine manufacturers and dealers, tooling suppliers and material manufacturers, signmakers can meet their clients’ needs with the best approach for any application.
Daniel Austin is general manager (GM) of MultiCam Canada, which supplies CNC router, plasma, laser and waterjet cutting systems and digital finishing systems. This article is based on a webinar he presented to membersof the Sign Association of Canada (SAC) earlier this year. For more information, visit www.multicam.ca and www.sac-ace.ca.