Managing colour from one place
For commercial print, packaging, and wide format to be printed in the same facility, colour management must be able to match to a print standard on press. This does not mean matching a wide-format inkjet printer to another wide-format printer or an existing traditional press. It is imperative to match both traditional and digital print processes and devices to a common reference that is easily accessible to print data suppliers, using generally known methods.
The practical operation of multiple colour management systems from different vendors running a variety of output devices on multiple media can be daunting. The user interfaces and results are often different when setting linearization, ink limits, rendering intents, etc. The less standardization that exists between different print devices, the more likely things can go wrong—and they often do.
A centralized colour management system with consistent print and process control tools offers exceptional control for printing on a variety of devices. While a centralized colour management system assures all print devices will match, it does not mean other systems are imperfect. It just means using non-centralized systems could produce different results unless meticulous care is taken to ensure settings are always aligned on all systems, all the time.
Centralized colour management can also offer additional benefits such as resolving Portable Document Format (PDF) flattening, transparencies, and overprint issues with centrally administrated settings, assuring
the same results. This also reduces errors in interpretation between the proof the customer sees and the final print job.
If one is lucky, he/she can find a colour management system to create unified calibration, and profiling tools that require very little user interaction to achieve colour quality and consistency across all devices. Combining calibration, profiling, transformation (e.g. red, green, and blue [RGB] to cyan, magenta, yellow, and black [CMYK]), and proofing technologies together is the first step to guaranteeing colour consistency and a superior print finish. It directs the operator easily through step-by-step wizard-based technology to create high-quality calibration, as well as creating a unique profile for the substrate being used.
Some systems can provide both colour and workflow controls, all on one station. It is much easier to operate a single application very well than to operate a variety of systems marginally.
Maintaining a standard
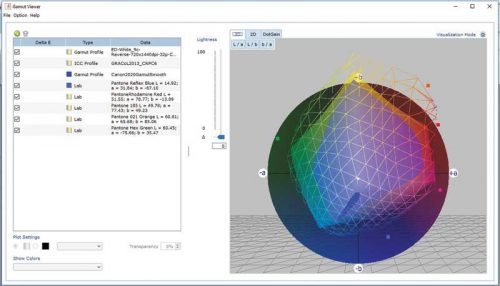
When looking for common appearance, a more sophisticated, gamut mapping strategy is needed because a major project could include printing on textile, a coated paper sheet, and a rigid plastic.
Using centralized colour management, a file is created in a colour standard space, such as General Requirements for Applications in Commercial Offset Lithography (GRACol). The centralized system converts that colour automatically to the colour space of the desired printer, whether digital, inkjet, toner, or conventional (e.g. screen or offset) processes.
Different devices can actually have a common appearance as long as the correct profile calculation algorithms are used. When looking for common appearance, a more sophisticated gamut mapping strategy is needed because a major project could include printing on textile, a coated paper sheet, and a rigid plastic. A sophisticated tool is required to map any common target colour space to each of those different print technologies and substrates. Of course, spot colours need to be accurate, predictable, repeatable, and controllable if they cannot be reproduced given the gamut of the device.
The big consideration is what target colour space should be used: GRACoL, Specifications for Web Offset Publications (SWOP), standard red, green, and blue (sRGB), or others—or does a house standard need to be matched? One needs to choose a common standard for a common appearance, while also maximizing the capabilities of the equipment. Using a centralized engine strategy to adapt a standard to printing conditions is critical to be able to reproduce intended colour and preserve it across common materials and print processes.
A common practice of commercial printers is to invest in G7 certification, tools, and consultancy in an effort to achieve a common grey balance across devices and substrates. For many, it is the first experience into ‘real’ process control, working with a spectrophotometer to make sure colour looks correct—and learning that measuring densities, LAB values or linearizing CMYK is simply not enough.
Basically, G7 calibrates the grey balance and tonality of CMY inks, as well as the tonality of the black channel. The G7 calibration works fairly well to keep the grey axis very stable, but when it comes to a highly saturated special colour, it depends on where the colours of the printer actually fall. While G7 calibration is better than most, one does not want to look at just the greys, but also the achievable gamut and repeatability of the printing technology. The larger colour gamut of wide-format printers offers challenges and opportunities.
Wide-format printers can produce much more vibrant colours than their offset- or toner-based counterparts, so limiting their colour gamuts to an offset GRACoL standard may not achieve the desired ‘pop’ the print buyer is looking to achieve. At the same time, some common appearance with other printers or project pieces may be required.
The right colour management tools make the best use of this wide gamut. The objective is a methodology that allows a fairly standardized way of working with CMYK documents (files where the gamut has been reduced, using a limited standard such as GRACoL), as well as files that have preserved a larger gamut (such as RGB formats), and custom colours (such as Pantone, or customer specified reference).
Only a proper colour managed PDF workflow allows the correct interpretation of all these files simultaneously when combined with well-profiled or standardized output devices.