Getting colour right when printing more than signs
A centralized workflow: Making colour management simple
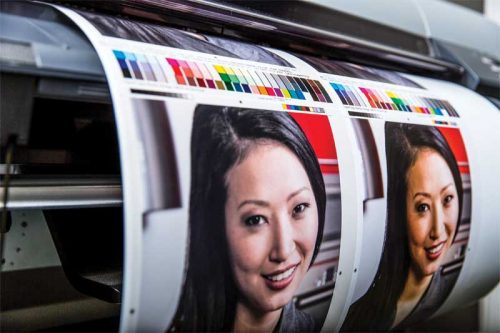
Illumination
The first step of a centralized system shuts off colour management on all RIPs in the facility. They will receive colour-managed files, so they do not need to perform this function. However, the RIP still performs basic screening and separation of the file to the output device needs.
Next, the target colour space needs to be selected and the print processes calibrated to make sure they are consistent. Otherwise, the devices are not going to match each other. Calibration is a key component. This involves not only printing a tone scale for each colour, but an entire test chart with patches also for all overprints of the available printer gamut, measuring them, and making adjustments to optimize the match between requested and printed values.
When the software has been updated and calibrated, how does one know it is correct? While some people perform calibrations regularly, it still needs to be verified. Calibration is basically a match of the colours of how they are supposed to be. This means using a spectrophotometer to verify colours are matching the exact colour they are supposed to print. This machine should be in a consistent state where it can return to next week, next month, or next year.
Once the calibration has been verified, it is time to build the profiles. It is how one can be predictable. While a good colour management system will have built-in grey adjustment similar to G7 offset systems, calibration from some colour management systems may not represent a good colour space. Printers typically want to create a profile for every output device to ensure they can obtain pleasing and predictable colour.
This involves creating a reference or ‘profile’ of the printer or press. A reference chart is printed and read with a spectrophotometer. This allows the software to understand what colours the printer can reproduce, as well as how it produces them. Good colour management software takes the printer colour output, compares it to the preferred standard (e.g. GRACoL CMYK or spot colour reference), and creates a link to correlate the printer’s colour capabilities to the colour target. Printers with a broader range of colours (gamut) support a better match to the colour standard or original colour being matched.
That said, colours do not have to be ‘dumbed down’ to the target colour space. A customer’s important brand colour does not have to be mapped into the standard GRACoL CMYK colour space. It is going to use any extra colour that one can get out of the printer to hit it as close as possible.
Note: Some colour technologies operate a bit differently than ICC. The big benefit is the quality of a separation. Device link technology separations can be much smoother in tonality, of a much higher quality while providing a better means of device-to-device matching with added benefit of ink savings.
Manage colour from one place
Therefore, when using centralized colour management, also known as a colour server, one will achieve consistent quality across all devices—conventional or digital presses—day in, day out, without having a lot of interaction with the production systems. This guarantees no matter what a client wants to produce, and no matter when they ask for it, a printer will always be ready to provide consistent, high-quality colour.
Erik Schmitt is director of sales, Canada, and wide-format product specialist, GMG Americas. He can be reached via e-mail at erik.schmitt@gmgcolor.com. Ryerson University is hosting a Specialty Graphic Imaging Association (SGIA) colour boot camp in June, showcasing GMG PrintFactory and ProofControl. For more information, visit www.colormanagement.com.