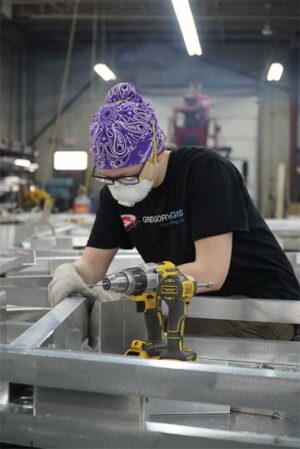
The team began with the construction of the face, followed by the back and, lastly, the steel structure that would support the sign.
No challenge too big
The project took six weeks from planning to installation with a lot of detailed thinking going into the design, engineering, and transportation of DSV’s sign. Questions as to how to build the sign with hidden components so it could withstand significant wind impacts without collapsing; how to move it from the shop floor to the transport vehicle; and, finally, how to transport and install it in a tight space under an overhang had to be precisely answered before fabrication could begin.
A thorough site check, meticulous calculations, and plenty of collaboration provided the necessary details required to design the sign to fit on top of a 12.2-m (40-ft) foundation built to withstand significant environmental stresses and the massive weight of the sign.
Due to the sign’s size and weight, the team decided to build it in one spot on the shop floor. Completing the entire project in one area presented a number of new obstacles.
To tackle these challenges, the team began with the construction of the face, followed by the back, and lastly by the steel structure that would support the sign. To ensure the greatest structural integrity, the fabricator built the hidden steel support underneath the face so the seams would be over a solid base and easier to sand and buff out. Once the pieces were put together, the full weight of the sign had to be lifted and put on its back so the face could be painted over a four-day period.
Every department worked closely together to build the sign and execute the first phase of the plan perfectly. With the fabrication completed, it was now time to face the challenges of transporting the sign to its new home in Milton.
Delivery day
One of the neat engineering parts of the DSV sign structure, was how to move it out of the shop on the day of installation. The team had to make sure the sign would fit out the shop door, and then tackle how to transport it (vertically or laid flat). There was a lot of measuring, calculating, and conversing between the teams to accomplish this.
The fabricator designed and built three sets of temporary wheels for the sign so it could be wheeled out of the shop standing straight up. It rolled easily—almost too easily—and great care had to be taken not to push the sign too hard or it would speed away. Moving such a large and heavy sign with such ease was, at the same time, both stressful and impressive.
The team knew the sign was over height and too high for the trailer, and transporting it on an angle would have required a special frame. In the end, it was decided the best way to ship the sign was to lay it flat. This presented challenges, however, as it had to be laid down on its face because of the steel structure on its back. Further, the sign had to be packed properly and the weight distributed precisely so there would be no damage to the face and fresh paint. It took three hours to pack the sign, and the install team worked closely with the fabricator to make sure all the hook up points were strong enough to lift the sign onto the trailer.