By Dean Derhak
When sign shops and other large-format print service providers (PSPs) are surveyed with regard to how much their ink costs per square foot of printed output, two out of three shop owners say they do not know. And when asked how much ink they waste in their production processes, again, few actually know the answer. Some even admit they would rather not know, lest they discover the depressing truth about lost profits.
Under these conditions, effective colour management and media profiling can help large-format PSPs cut their ink costs. Tracking ink use, specifically, can lead to increased profits.
Calculating costs
Understanding ink costs is just a good, basic business practice. It can help a sign shop better quote its jobs while reducing ink use and waste. A typical print shops that spends $35,000 per year on ink can learn to reduce its use by 15 per cent, leading to additional profits of $5,250 per year. Smarter colour management may save even more.
Calculating average ink costs per square foot of printed output is easy. It is simply a matter of dividing the cost of ink used over the course of a month by the total area printed during that same month.
First, these figures need to be tallied. Most of today’s raster image processor (RIP) software packages offer a job log, which measure the area printed by tracking substrate use. Some RIPs show the total printed area per job, while others only indicate the width and height, thus requiring the user to manually calculate the area.
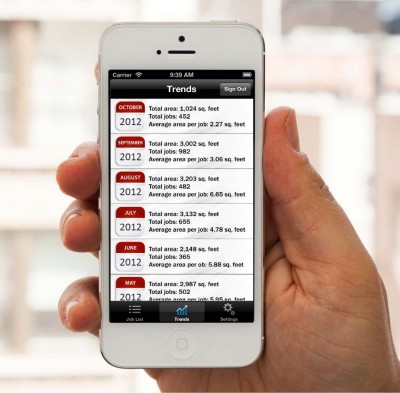
Today, mobile apps can track substrate use and indicate total print area per job. Photo courtesy SAi
There are also other ways to determine these figures. Some printers have built-in web servers that indicate print area per job. There are even apps now that can display this information on smart phones and other mobile devices.
Tallying ink costs, meanwhile, merely requires the shop owner to count how many ink cartridges are used up over the course of the month and then multiply that number by the price per cartridge.
By way of example, a sign shop might print 44.6 m2 (480 sf) of output in one month and pay $390 for the ink used by these graphics. This means the average cost is $8.74 per square metre ($0.81 per square foot)
Importantly, this formula factors in any unused or wasted prints. It also takes into account any inkjet printhead cleaning and purging. What this means is the shop can work out its true costs of ink per square metre, not just the costs of regular ink use itself. The factors that matter most are how much is spent on ink and then how much is actually printed.
Some shops, for example, quote all jobs with a single per-square-foot cost, but not all jobs use the same amount of ink. When shop owners truly understand ink costs, on the other hand, they can quote jobs based on low, medium and high ink use, so as to ensure profits on each type.