Ensuring effective colour management
When a wide-format PSP is starting up, it is essential to obtain the right ICC media profiles. A surprising number of shops mistakenly use one generic media profile for all of their substrates. Then, in the event of a problem, they use colour correction adjustments in their software. Not only does this practice waste a tremendous amount of ink—often without the printer operator realizing it—and thus escalate costs unnecessarily, but it also makes spot colour matching much harder.
So, it is important to set up ICC profiles for each printer and substrate. Then, the matching profile can be selected each time a printer’s operator changes media.
Getting the profiles is very easy, as they are typically available from printer manufacturers, substrate suppliers and RIP software developers. For complete control, however, it is better to develop one’s own ICC profiles. While this requires additional upfront training and costs, the investment will pay off over time, as the shop staff will know best how to reduce ink costs during production while maintaining customer satisfaction with the end product. High quality, after all, is whatever customers say it is.
Using the right inks
One good way to start reducing costs is to avoid ‘light ink’ use. Wide-format printers equipped with light magenta and light cyan inks—which are formulated with less pigment and more clear liquid than regular inks—tend to use them a lot, even when they are not needed.
The sole purpose of these light inks should be to improve image smoothness for close-up viewing, but the effectiveness of this technique depends on the application and its required viewing distance. Most wide-format graphics in the sign industry, after all, are not designed for close-up viewing.
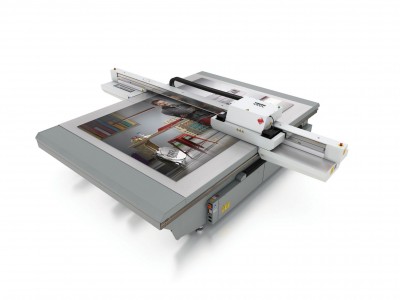
It is important to set up ICC profiles for each printer and substrate. Photo courtesy Océ Display Graphics Systems
Reducing the use of light inks can save up to 25 per cent of annual ink costs. The colour gamut will not be heavily affected, as dark colours will still be dark and the grey balance will be maintained, even if images look less smooth up close.
Another cost-reducing technique involves producing grey and black in different ways, using the grey component replacement (GCR) curve control in the software used to make ICC profiles. Most default ICC profiles use a lot of cyan, magenta and yellow (CMY) inks when printing greys, but this process consumes up to two-thirds more ink than necessary.
The setting will depend on the media—backlit prints, for example, require a lot of ink anyway—but selecting a GCR curve that replaces CMY inks with black ink when printing grey and black can reduce costs substantially, with little negative impact on printed graphic quality. And even with some loss in detail, this option will deliver richer blacks.
Some ICC profile software engines even have ‘Max K’ settings that replace CMY with key/black (K). This technique can potentially save another 20 per cent of ink use per job.
The disadvantage with this technique is upon close-up viewing, small black ink dots—known as ‘peppering’—may be visible in the graphics’ highlight and mid-tone areas. Also, if this technique is overused, the colours could be ‘blown out,’ reducing some detail in shadows.
Again, where the levels should be set will depend on the media and on the intended viewing distance, so it is essential to experiment a little first to ensure customers will be satisfied with the results. In any case, the technique is definitely worth considering, as it can dramatically reduce costs.