Solvent inkjet printing
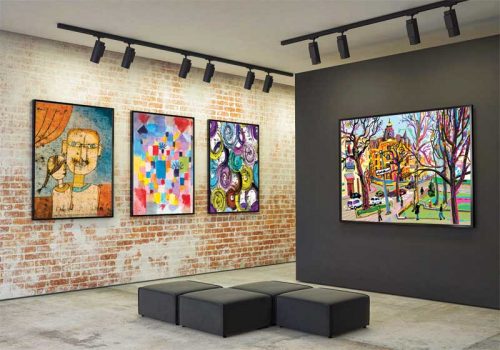
The world of large-format printing continues to evolve. As new technologies come to market, demands for these solutions are also increasing.
In reality, commercial print providers need a combination of technologies to stay competitive.
Solvent inks are generally pigment inks. They contain pigments rather than dyes, but unlike the aqueous version where the carrier is water, in solvent inks, the carrier is volatile organic compounds (VOCs).
The main advantage of solvent inks is they are comparatively inexpensive and enable printing on flexible, uncoated vinyl substrates. Unlike aqueous inks, prints made using solvent-based inks are generally waterproof and UV safe (for outdoor use) without special over-coatings. Solvent can offer excellent vibrant colours, albeit often not as strong as aqueous dye or pigment inks.
A key benefit is the durability of the print, which offers excellent outdoor life. Hard solvent ink offers the greatest durability without specialized over-coatings, but requires appropriate ventilation of the printing area to avoid exposure to hazardous fumes. Mild or eco-solvent inks, while still not as safe as aqueous inks, are intended for use in enclosed spaces without specialized ventilation of the printing area. Mild solvent inks have rapidly gained popularity in recent years as their colour quality and durability has increased while ink cost has dropped significantly.
Strengths
Solvent printers produce a very durable, scratch-resistant product that is typically used for outdoor applications. They print on uncoated materials and essentially “etch” the surface of the material to bond securely to the substrate.
Limitations
As a result of VOCs and fumes, solvent machines require excellent ventilation. Complete drying can be an issue for media that needs to be finished, specifically lamination.
Solvent inks also need to allow for outgassing. This is the time it takes for the carrier elements in the ink to leave the surface of the material. The recommended time for this process before lamination is anywhere from several hours to a day; this leads to a very labour-intensive process for each print when considering finishing times needed for laminating, storing, packing, and shipping.
Key applications
- promotional signage;
- floor graphics, stickers, and repositionable graphics;
- backlit displays;
- interior decorations or wallcoverings; and
- vehicle wraps.
UV gel inkjet printing
UV gel technology combines a radically new UV-curable ink that instantly gels on contact with the media, an advanced “self-aware” piezoelectric print head technology, an LED-based UV system that cures without adding any damaging heat to the media, and continuous, on-the-fly, print head nozzle monitoring and performance compensation.
UV gel ink does not contain water, which also significantly helps to reduce media swelling, improving dimensional consistency. This gives excellent results for applications requiring multiple tiled panels, such as wallcoverings. Prints are durable, lightfast, and abrasion-resistant, which makes them suitable for demanding outdoor applications.
This ink has been developed to be nearly odourless and ultralow in VOCs, so prints are ideal for sensitive indoor environments. The flat profile of the UV-gel dot produces smooth prints that are easy to laminate straight off the printer for heavy-duty applications. Inherently, these prints are highly resistant to environmental stresses, which minimizes the need to laminate for all but the most demanding applications.