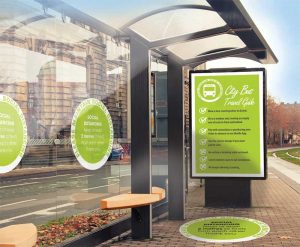
Keeping floor graphics clean and well-maintained is very important for safety, as dirt will obscure the message while spillages may pose a tripping or slipping hazard.
Installation and maintenance
Once the correct floor graphics media has been purchased, printed, and finished—one that is compatible with the ink chemistry, conditions, and project duration, and one that ticks all the relevant boxes for slips, trips, and fire safety—it is now essential to install them correctly. Many floor graphics products are designed to be easy to apply, even by a non-professional, so choosing these will ease this process. There are how-to videos online to guide installers through the application process step-by-step, including advice on preparation. Standard procedure is to clean the floor surface, then dry it thoroughly before applying the decal.
How-to videos will also list any tools required. For print-and-go products, nothing more is needed than a squeegee to release air bubbles, but for two-part products, installers may find a heat gun beneficial for getting decals seriously secure. Heat softens adhesive and makes polyvinyl chloride (PVC) more flexible to fit into crevasses in a floor’s surface, providing a better bond. Similarly, a heated laminator can make thicker laminate products more pliable. Some may want to use a sealant around the edges of a floor decal or on overlapping seams to secure graphics more thoroughly and protect from cleaning.
Keeping floor graphics clean and well-maintained is very important for safety, as dirt will obscure the message while spillages may pose a tripping or slipping hazard. However, using the correct cleaning products is necessary to avoid causing damage, so always check with the media manufacturer or supplier and the cleaning product label to ensure compatibility. As a general guideline, agents containing two to five per cent bleach, used to disinfect surfaces, are suitable for the PVC, polypropylene, polyethylene terephthalate (PET), and polychlorotrifluoroethylene (PCTFE) films used in the majority of graphics overlaminates. Some organic solvents and ammonia-based cleaners may damage certain films so they should be avoided unless advised otherwise.
Cleaning will also weaken the adhesive of a floor decal and, in turn, increase its trip hazard potential. Owing to their horizontal position, floor graphics will be exposed to cleaning agents for longer than a vertical display, so special care should be taken, and exposure should be limited, along with ensuring a safe cleanser is used. As mentioned earlier, two-part laminated decal products are better suited to environments that use industrial cleaning and buffing machines.
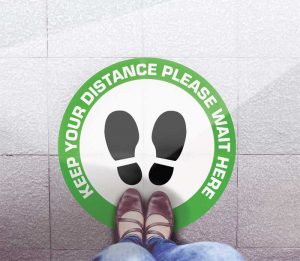
Floor graphics that are used to convey a message—safety instructions or directions, for instance—must have resistance against colour fade, loss of ink adhesion, and abrasions and scratches.
Keeping people safe
With so many factors to consider, it is important to remember floor graphics are being used in the real world to help keep people safe—often on a large scale. For example, in London, U.K., social distancing notices have been rolled out across the public transport network, a vast project that had to be completed not just accurately, but also quickly. Over the course of 10 days in May 2020, local business FD Signs printed, finished, and delivered approximately 100,000 social distancing floor graphics for installation by 30 different teams in London Underground, railway stations, and tram stops. To produce the bold blue and white circular decals, FD Signs used a Fujifilm Acuity LED 1600 UV printer and a Drytac two-part graphics solution using a specialized polymeric self-adhesive PVC film with a 4 mil (100μ) monomeric soft calendared laminate. This product is rated for fire safety in public spaces and is slip certified. These decals remained secure and legible despite heavy foot traffic as commuters began heading back to work. This highlights the importance of using the right floor graphics product for the job.
The market for floor graphics is set to expand, but businesses should not see them as just another display job. Suppliers must talk to their customers through every detail to ensure their needs are met—not just now, but in two, six, and 12 months—and people are kept safe.
With almost 10 years of experience with Drytac, David Morgan currently serves as technical assistant. With his excellent technical knowledge of chemistry and thorough understanding of the graphics market, Morgan offers sound advice on both products and applications. For more information, visit www.drytac.com.