1950s
Of course, neon already offered bright colours and free-form design possibilities, which helped retailers, marketers, restaurants and other businesses establish their own unique looks. In the early 1950s, acrylics began to displace painted metal as a substrate for neon signs. With their integral colour pigments, they eliminated the paint deterioration that was common to metal faces, particularly in severe climates.
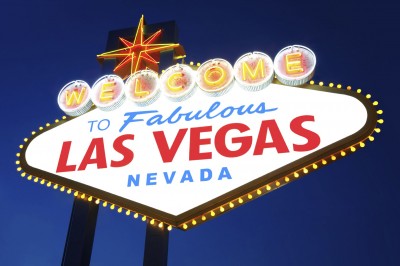
With the advent of acrylic sheets, translucency enabled neon sign backlighting for brighter messages at night.
Acrylics also offered greater design versatility, production benefits when making multiple signs and easier installation. A variety of translucent colour options allowed the internally backlit materials to achieve strong visual appeal at night with brighter messages. The integral pigments added longevity. That said, severe weather conditions—including high winds and hail—led to breakage, highlighting the shortcomings of acrylic signs in certain locations.
Translucent plastic sign faces worked well with neon. This combination found its way into both flat and thermoformed signs. At the same time, retail, restaurant and hotel chains were expanding, creating a greater need to produce larger numbers of signs sharing the same design, branding and colours. Plastics filled this need because they were easier to formulate and fabricate with consistency.
In addition to this expansion of signage, there were two distinct physical advantages of plastic sheets that furthered the growth of their use: large sheet sizes facilitated the production of larger signs in diverse shapes; and low weight made the installation of these larger signs less expensive than metal signs.
The production of larger sign faces, however, increased the risk of breakage during production, shipping and installation (particularly in cold weather). Also, with regard to breakage, the growing popularity of ground-level illuminated signs for directional and marketing purposes led to an increased risk of damage from vandalism.
Such problems during this phase drove further development of polycarbonates for signs. Resins were quickly adapted for sheet extrusion to help prevent breakage problems for sign faces. The sign industry turned to polycarbonate sheets that had originally been developed as clear, impact-resistant materials for safety glazing in architecture.
1960s and 1970s
While acrylic products continued to proliferate with new colours, sizes and patterns, polycarbonate sheets came into widespread use in the 1960s across North America, as suppliers promoted the materials’ resistance to impacts and breakage. Soon, polycarbonate manufacturers achieved multiple colour options that had been established for acrylics. Suppliers educated signmakers about thermoforming, fabrication and decoration techniques specific to polycarbonates.
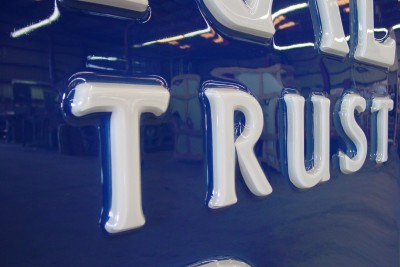
The integration of co-extruded ultraviolet-resistant (UV-resistant) polymer cap layers into polycarbonates eliminated outdoor weathering issues.
Within a few years, however, the sign industry learned polycarbonate, like acrylic, had its limitations. Especially in environments with intense ultraviolet (UV) light, sign applications revealed polycarbonates would lose their gloss and vibrant colour over time.
To remedy this shortcoming, plastic sheet suppliers developed a film cap layer for polycarbonates that could be applied during the extrusion process. This proved a partial success, but encountered forming issues in deep-draw faces. The film cap also delaminated in certain environments.
A more effective solution to the weathering problem came along when manufacturers developed a co-extruded UV-resistant polymer cap layer. This technology integrated a new layer of UV-absorbing resin into the surface of a polycarbonate sheet, eliminating the earlier issues of delamination during forming or use.
Indeed, this technology remains the standard for polycarbonate sign products today. There have been decades of successful applications using UV-resistant grades of plastic.