Static signage
As a key visual landmark for consumers, bright and evenly illuminated outdoor signage is crucial to the brand images of countless businesses and stores. There are many ways to illuminate a sign by day and night, including not only LEDs, but also more traditional neon, fluorescent and electroluminescent (EL) systems. There are also different techniques for lighting signs, including from the back, from the front, along the edges and the aforementioned halo lighting (whereby light reflected from behind a sign illuminates its silhouette).
While neon and fluorescent lighting are still fairly commonly used around the world today and can serve their purpose effectively for many years, LEDs have proven a strong alternative for the illumination of channel letters, lightboxes and other backlit signage applications. Indeed, they may well signal the eventual demise of the older lighting technologies.
LEDs offer an array of benefits for illuminating signs, including reliability, ease of installation and energy savings. Even HB LEDs are low-voltage and can be operated with low running costs, making signs both brilliantly bright and energy-efficient. LEDs also offer increased longevity over traditional forms of lighting, reducing maintenance costs over the life of a sign.
“LED lighting offers several improvements for outdoor signage lighting compared with standard fluorescents,” says Mark Shephard, global product manager for General Electric (GE) Lighting, “from significant energy cost reductions and easier job-site installation to less frequent maintenance and more consistent brightness to better uniformity and cold weather performance.”
Metal or acrylic sign letters can be front- or rear-illuminated with LEDs or halo-illuminated for a more subtle, esthetically pleasing effect. LEDs can also be used to edge-light acrylic panels, which can be installed independently as ‘light sheets,’ connected as ‘light walls’ or integrated into aluminum frames to serve as ultra-thin lightboxes.
Traditional aluminum lightboxes have been effective for decades and remain very popular today, as they are as simple in design and construction as their name suggests; i.e. a box is illuminated from within. When fabricated in the traditional manner, however, lightboxes consume excessive quantities of energy. A typical large-format lightbox may measure 6 x 3 m (20 x 10 ft), for example, and will require 45 58-W fluorescent tubes for effective illumination. Even if it is operated for only 12 hours a day, it will consume approximately 12,000 kW of electricity per year, for an annual electricity bill in excess of $1,000.
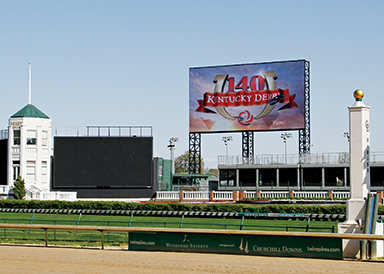
In April 2914, Churchill Downs – known for the annual Kentucky Derby – unveiled the ‘Big Board’ which is named the world’s largest 4K LED-based video board by the Guinness World Records. Photos and figures courtesy ElectroniCast Consultants.
Another problematic issue for traditional aluminum signs is maintenance. If just one fluorescent tube is faulty, the sign will present its graphics poorly. And with 45 or more tubes in a single sign, the likelihood of such a fault, at any given time, is rather high. Flickering and/or broken tubes can quickly represent significant ongoing costs in terms of sign maintenance.
The flexibility and ease of installing LEDs makes them ideal for the on-site retrofitting of existing illumination systems for channel letters, lightboxes and backlit signs. There is often no need to remove or replace the sign.
In terms of flexibility, with a bending radius of less than 1.3 mm (0.05 in.) and a life cycle of more than 500,000 bends, LEDs can be installed at practically any angle, following the tightest channel contours, all in one continuous strip and using only one or two connectors per letter.
With power consumption averaging only 0.8 W per linear foot, LEDs are indeed a very efficient lighting system, allowing two or three average channel-based signs to use the same amount of electricity as a single 100-W incandescent light bulb. And with the addition of a photovoltaic system to collect and store solar energy, some signs can even be illuminated independently without a direct connection to any traditional power source.
It is notable that specific LEDs have been developed especially for channel letters, lightboxes and backlit signage applications. Ultra-high-intensity semiconductor chips are uniquely packaged to ensure uniform illumination with a wide light-emitting angle. As a result, most 203-mm (8-in.) stroke channel letters can be illuminated using single rows of LEDs, without creating visible ‘hot spots’ (i.e. areas brighter than others), in depths as low as 63.5 mm (2.5 in.).
Many new LED systems have been designed as replacement kits for upgrading fluorescent-illuminated sign boxes and cabinets, providing anywhere from 58 to 76 per cent energy savings over T12 high-output (HO) fluorescent lamps. They are available in a wide variety of sizes and colour temperatures, offering the versatility necessary for signmakers to improve the overall esthetics of a multitude of single- and double-sided sign sizes and styles. Some can use existing fluorescent lamp sockets for quick installation, reducing labour time and costs.
Another factor is optics. Lens technology has been configured to help ensure light is emitted as efficiently as possible, while also protecting the LEDs themselves against moisture, humidity, damage and corrosion.
Fluorescent lamps emit light in a 360-degree pattern. With LEDs, on the other hand, each module is shaped to capture otherwise wasted light and redirect it where it is needed, i.e. toward the surface of the sign. Optics are key in eliminating the striping and shadows on the sign face that can occur with fluorescent tubes.