Preventing silvering of overlaminates
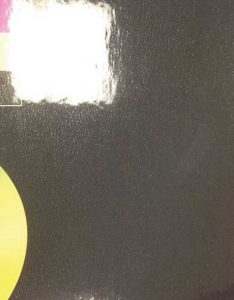
How can operators reduce silvering on their graphics during the laminating process?
Temperature
A warm pressure-sensitive adhesive will flow over a surface easier than a cold one. Most laminators have a heated top roller to improve adhesive flow. When employing this method, moderation is the best practice.
Using too much heat on a roll of laminate will cause shrinkage for certain films. Additionally, inks may start outgassing and adhesive can break down. It can also induce sheet curl to the graphic’s liner.
The optimal temperature for pressure-sensitive laminates is between 32.2 and 43.3 C (90 and 110 F), and the maximum level of heat is 54.4 C (130 F). The operator should allow the laminator’s temperature to stabilize after temperature adjustment, before starting production. This may take 10 to 15 minutes. During warmup or cooling, it is important to turn the laminating rolls for uniform roll temperature.
Pressure
As the name implies, a pressure-sensitive adhesive will flow better as the pressure increases. Most commercial laminators have hydraulic or air cylinders to apply pressure between the laminating rolls. Similar to temperature changes, moderation is required. The optimal laminating pressure is 275.7 to 551.5 kPa (40 to 80 psi). A general rule of thumb is to use less pressure with thicker overlaminate films, as opposed to thin films.
Tension and speed
Tension and speed are interdependent in the laminating process. Air bubbles are an indicator of insufficient tension on the laminating film in relation to the graphic. Silvering means fine amounts of air are getting trapped between them, so tension on the lamination film should be one of the first variables investigated. Another general rule is that as lamination speed increases, tension will need to increase, to maintain a flat lamination.
Further, as film thickness increases, tension will also need to increase, to maintain a flat lamination. An immediate curl off the laminator is a primary indicator the tension is drastically unequal to the speed, with one being too high in comparison to the other. Silvering in a flat lamination indicates the tension is close to optimal, but the pressure and the speed should be adjusted. Slowing down the laminating speed will increase the time the adhesive has to flow under pressure and squeeze the last bit of air out of the valleys of a rough print, which will reduce silvering. The optimal laminating speed for pressure-sensitive laminates is 0.6 to 1.5 m (2 to 5 ft) per minute.
It is important to keep in mind the guidelines above are general operating settings. For any specific recommendations, an operator should consult with their laminator’s manufacturer.
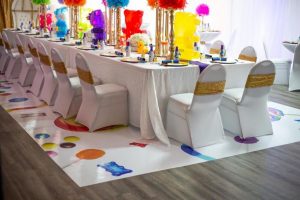
Conclusion
With the large variety of print methods and the ever-expanding creativity of graphic designers seen today, it stands to reason that print service providers and laminator operators will continue to encounter an infinite combination of challenges when it comes to laminates and silvering. When a print has a rough surface finish and predominately consists of dark or saturated ink coverage, there is a high possibility the image will exhibit some silvering. Fine amounts of silvering may dissipate from 24 to 48 hours after lamination, as the pressure-sensitive adhesive continues to wet out the print surface. However, moderate to heavy initial silvering will require changes to the process and potentially reworking the whole project. With this knowledge, the operator really needs to inspect the first laminated pieces for silvering and, if it is detected, follow the recommended troubleshooting measures above. These recommendations will help to control costs, eliminate rework, and produce the smoothest, silvering-free lamination, so companies can deliver the best possible product to their customers.
Jay Kroll is a product manager at General Formulations, a manufacturer of pressure-sensitive solutions for the graphics industry. His focus is on cut vinyl, transit, and wall graphic applications. Kroll has been designing and developing various manufactured solutions for more than 20 years in the medical, aerospace, specialty tape, and graphics industries.