Preventing silvering of overlaminates
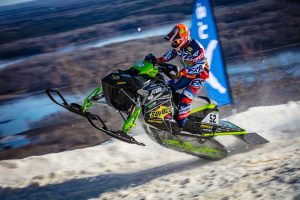
By Jay Kroll
Decal applications commonly require an overlaminate film to provide protection for a graphic, extend its useful life, offer some specific functionality, or enhance the overall look and feel of the material. Each project can call for slightly different products, depending on finish, durability, and application.
On very rare occasions, these overlaminates will be applied by hand, but the most common and effective procedure for applying an overlaminate film to a graphic is by using a dedicated laminator. Typical methods include liquid lamination; hot lamination, which uses a film with a heat-activated melt or adhesive layer; and cold lamination, which uses a pressure-sensitive adhesive to achieve a bond with the base material. The discussion below will focus on the latter process, cold lamination. This method is accomplished by running the graphic and laminate between two rolls under pressure, sometimes with low heat, to assist with adhesive flow.
Laminators can vary in width up to 1,651 mm (65 in.) and some can accommodate rolls of laminate more than 304.8 m (1,000 ft) in length. Operators can compensate for thickness by controlling the speed and tension of the individual film rolls travelling through the laminator. The media chosen will determine the gap needed between the rollers or nip setting. The speed and tension—and on certain laminators, the pressure—will need to be adjusted accordingly.
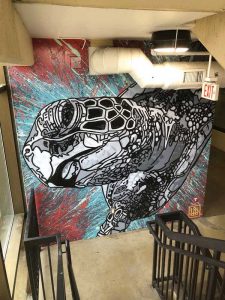
What causes silvering?
Lamination is a mechanical process and adjustments must be made continually, depending on the topography of the graphic. Most problems with lamination are a function of tension, pressure, heat, or speed. One common issue is air becoming trapped between the graphic and the laminate, which can manifest itself as large, visible bubbles in the worst case, or fine entrapment of air at the micro level. This phenomenon is called “silvering.” When large bubbles are present, it is often a function of tension and pressure, and it is very visible, which makes the problem easier to observe and be corrected quickly. However, since silvering is very fine, it can be difficult to detect and can go unnoticed during a laminating run, because of the subtlety of the small bubbles.
During the lamination process, the adhesive of the overlaminate must come into direct contact with the contours of the printed surface of the graphic. Total contact with the surface allows for an unobstructed view of the fine detail and colour of the graphic through the overlaminate to the observer’s eyes. When small pockets of air are trapped between the adhesive of the overlaminate and the printed surface of the graphic, these create small disturbances in the image that will distort the graphic to the observer. This disruption slightly scatters the light waves, creating a white appearance. It is easily observed against a dark background as a flecked or salt crystal form, hence the term “silvering.” It can exist against a lighter-coloured background, but without the colour contrast, it is much more difficult to observe.
What types of graphics are most likely to induce silvering?
Graphics with rough surfaces are more likely to exhibit silvering over graphics with smoother surfaces. A rough surface can be caused by something as simple as the texture of ink on the media, which is typically found with ultraviolet (UV) cured inks. When printing with a large quantity of ink for a graphic that requires a higher saturation, roughness may occur, because more ink dots are required to achieve certain colours. All digital printers use a minimum four-colour printing process, which means any high-ink-density print has the potential to develop silvering. For example, four-colour screenprints have comparatively large ink dots, so the process can also be particularly susceptible. To eliminate all micro air during lamination, the pressure-sensitive adhesive has to penetrate all the valleys between the ink dots. The larger the ink dot or the rougher the surface of the print, the harder it is for the adhesive to reach the valleys between ink dots, resulting in air entrapment at the bottom of each valley.