Preventive maintenance for inkjet printers
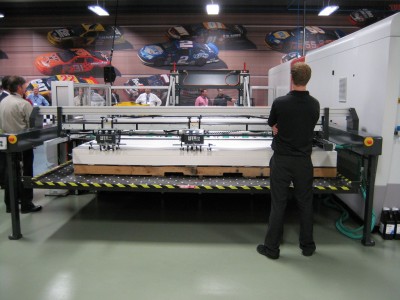
By Bob Flipse
Too often, by the time a wide-format inkjet printer is serviced, it is in a state of crisis that could have been prevented. While most drivers know to get their car’s oil changed periodically, many people still do not think about printers in the same way—despite the fact their printer, unlike their car, can make a lot of money for them. The need for preventive maintenance is not merely cosmetic—e.g. preventing operators from placing solvent-soaked cloths or splashing ink on the printer—but also, more importantly, mechanical.
Much like owning a car and occasionally taking it to an automotive specialist, printer owners can do their own ‘oil changes,’ performing basic maintenance in between major service intervals. Like a car, an inkjet printer contains critically important fluid systems that need to be kept clean for optimal performance and longer operating life. Unlike a car, where most such systems are sealed, a wide-format printer’s caps, capping maintenance stations and/or printheads are exposed to outside air and contaminants during—and sometimes after—printing.
The major components of a solvent-based inkjet printer are the media transport and take-up system, the carriage and positioning, the electronics and controls and, responsible for the most maintenance service calls, the ink system.
Checking components
Each printer has its own maintenance routine, but a number of practices will apply to almost any printer, regardless of its manufacturer. One way to consider how the technology works and what is going on throughout the printer is to work from the end of the system, back to the beginning.

The waste bottle is the end of the line, as it is where wasted ink goes after the printheads are cleaned, the nozzles are washed and/or the printheads are primed. The ink is pulled through the printheads and pushed into the bottle by way of a pumping mechanism. If the bottle becomes full or if the service line that feeds into it is gummed up, the printer can become clogged.
Most printers use a pull-through pump system that draws ink through each printhead to prime them and keep the ink flowing, but for this process to be effective, there needs to be a good seal between the cap and the printhead. Typically, the printhead has a flat surface and the cap is like a rubber boot that seals the connection.
If the seal is not good, air leaks may occur whenever the pump tries to pull ink through the printhead. When such leaks happen, the printhead will not be primed, as no ink can be pulled through it. And during cleaning cycles, air leaks will prevent the printhead from being cleaned.
There are several causes of cap/printhead seal problems. For one thing, rubber caps will deteriorate over time with constant exposure to solvents and heat. Old and worn-out caps should be replaced.
There may also be poor alignment of the caps and printheads. If the caps do not seal the printheads in the correct position, there will be air leaks. So, it is important to perform a capping station alignment.
There can be problems with the capping station motor. While the specifics vary from printer to printer, some models use motors or belts to raise or lower the caps during and after printing. If this process encounters a problem, the solution is to repair or replace the motor assembly or its affected parts.
Poor cap maintenance can result in dried ink and pigments crusting right where they need to be sealed, at the cap-to-printhead interface. Additionally, failure to keep the caps clean will result in much faster degradation, as the crust will become abrasive, at which point cleaning it with solvent and swabs can tug bits off of the cap, resulting in premature failure. It is important to swab the caps gently and regularly instead.